Главная
Популярная публикация
Научная публикация
Случайная публикация
Обратная связь
ТОР 5 статей:
Методические подходы к анализу финансового состояния предприятия
Проблема периодизации русской литературы ХХ века. Краткая характеристика второй половины ХХ века
Ценовые и неценовые факторы
Характеристика шлифовальных кругов и ее маркировка
Служебные части речи. Предлог. Союз. Частицы
КАТЕГОРИИ:
|
Фотографии установок первичной переработки различной конфигурации 4 страница

-------------------------------------------------------------------------------- Если исходное сырье не полностью осушено и десульфурировано, существует возможность образования кислоты, приводящая к отравлению катализатора и коррозии металла. Нельзя позволить, чтобы вода или пар попали в те места, где присутствует хлористый водород. Необходимо предпринять меры предосторожности для предотвращения проникновения HCl в канализационные коллекторы и дренажи. Имеется потенциальная опасность воздействия изопентана и паров и жидкости алифатической нафты, а также технического газа, обогащенного водородом, соляной кислоты и хлористого водорода, и пыли, когда используется твердый катализатор. Производство водорода (паровой реформинг) Водород высокой чистоты (от 95 до 99 %) необходим для процессов гидросульфурации, гидрирования, гидрокрекинга и нефтехимических процессов. Если производится не достаточное количество водорода как побочного продукта процессов нефтепереработки для удовлетворения общих потребностей нефтеперерабатывающего завода, требуется дополнительное производство водорода. При реформинге водородного пара десульфурированные газы смешиваются с перегретым паром и преобразуются в трубах, содержащих базовый никелевый катализатор. Газ реформинга, который состоит из пара, водорода, угарного газа и двуокиси углерода, охлаждается и пропускается через преобразователи, где угарный газ вступает в реакцию с паром с целью образования водорода и двуокиси углерода. Двуокись углерода очищается в скрубберах растворами амина и выбрасывается в атмосферу, когда растворы реактивируются путем нагревания. Любой угарный газ, остающийся в потоке продукта, преобразуется в метан. (См. Рис.78.17)
--------------------------------------------------------------------------------
Рис. 78.17 Процесс парового реформинга
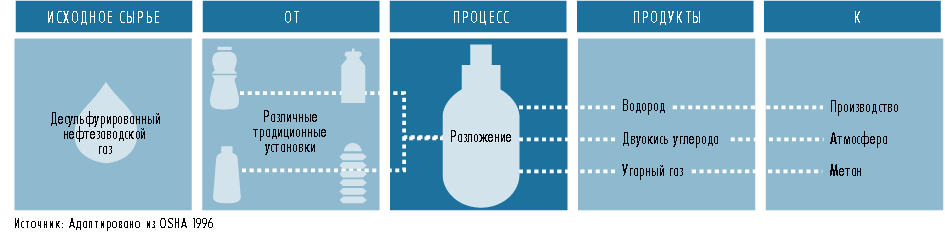
-------------------------------------------------------------------------------- Должны быть проведены инспектирования и испытания там, где существует возможность поломки регулирующего клапана вследствие присутствия загрязнителей в водороде. Должны контролироваться переносы потоков из щелочных скрубберов с целью предотвращения коррозии в подогревателях, и должно быть предотвращено поступление хлоридов от исходного сырья или паровой системы в трубы реформинг-установки и загрязнение катализатора. Воздействия могут произойти в результате загрязнения конденсата техническими материалами, такими как щелочи и соединения амина, и из-за излишнего водорода, угарного газа и двуокиси углерода. Существует потенциальная возможность ожогов горячим газом и перегретым паром, если происходит выброс. Разнообразные процессы нефтепереработки Процессы получения базовых компонент смазочного материала и парафина Смазочные материалы и парафин очищаются от различных фракций атмосферной и вакуумной перегонки. С изобретением вакуумной перегонки было обнаружено, что из воскового остатка получают лучший смазочный материал, чем из животных жиров, которые использовались на начальном этапе развития современной технологии переработки углеводородного смазочного материала, чья основная цель состоит в том, чтобы устранить нежелательные продукты, такие как асфальт, сульфонированные ароматсоединения и парафиновые и изопарафиновые воски из остаточных фракций с целью производства высококачественных смазочных материалов. Этого достигают с помощью ряда процессов, включая процессы деасфальтизации, извлечения растворителем и разделения и обработки, такие как депарафинизации и гидроочистки. (См. Рис. 78.18) -------------------------------------------------------------------------------- Рис. 78.18 Процесс производства смазочного масла и парафина

-------------------------------------------------------------------------------- Выделенный из гудрона жидким пропаном продукт объединяют со смазочным материалом прямого погона, предварительно нагретым и извлеченным из исходного сырья с помощью растворителя компонентом, называемым рафинатом. В типичном процессе извлечения используют фенол в качестве растворителя. Исходное сырье смешивается с фенолом в секции обработки при температурах ниже 204 °C. Фенол затем отделяется от рафината и рециркулирует. Рафинат может затем быть подвержен действию другого процесса извлечения, который использует растворитель фурфурал для отделения ароматических соединений от неароматических углеводородов и получают светлоокрашенные рафинаты с улучшенными показателями вязкости, окисления и термостойкости. Депарафинизированный рафинат может также подвергнуться дальнейшей обработке с целью улучшения качества базовых компонент. Глиняные адсорбенты используются для удаления окрашенных в темный цвет, неустойчивых молекул из базовых компонентов смазочных материалов. Альтернативный процесс, гидроочистка смазочного масла, пропускает горячий депарафинизированный рафинат и водород через катализатор, который слегка изменяет структуру молекул, создавая в результате светлоокрашенный продукт с улучшенными характеристиками. Обрабатываемые базовые компоненты затем смешиваются и/или соединяются с добавками с целью удовлетворения требуемым физическим и химическим характеристикам моторных масел, промышленных смазочных материалов и масел для металлообработки.
Два различных типа парафина извлекают из сырой нефти - парафин, произведенный из дистиллятных компонент, и микрокристаллический парафин, произведенный из остаточных базовых компонент. Рафинат из установки извлечения содержит значительное количество парафина, который может быть удален путем извлечения растворителем и кристаллизацией. Рафинат смешивается с растворителем, таким как пропан, метилэтилкетон (MEK) и смесью толуола или метилизобутилкетона (MIBK), и предварительно охлаждается в теплообменниках. Температура кристаллизации достигается с помощью испарения пропана в холодильной установке и резервуарах для подачи к фильтру. Парафин непрерывно удаляется с помощью фильтров и охлажденного растворителя. Растворитель восстанавливается из депарафинизированного рафината путем мгновенного вскипания и отгонки низкокипящих фракций водяным паром, и рециркулирует. Парафин нагревается с помощью горячего растворителя, охлаждается, фильтруется и окончательно промывается с целью удаления всех следов нефти. Перед использованием парафина, он может быть гидроочищен с целью улучшения запаха и устранения всех следов ароматсоединений с тем чтобы, парафин мог использоваться при изготовлении продовольствия. Депарафинизированный рафинат, который содержит небольшие количества парафинов, нафтенов и некоторые ароматсоединения, может далее обрабатываться для использования в качестве базовых компонентов смазочных материалов. Контроль над температурой установки обработки имеет важное значение с целью предотвращения фенольной коррозии. Парафин может засорять коллектор или системы дренажа и мешать обработке сточных вод. Существует опасность воздействия технических растворителей, таких как фенол, пропан, метилэтилкетон и смеси толуола или метилизобутилкетона. Вдыхание газообразных углеводородов и паров, ароматической нафты, содержащей бензол, сероводорода и технического газа, обогащенного водородом, представляет опасность. Производство асфальта После первичных операций дистилляции, асфальт - часть остаточного материала, требует дальнейшей обработки для получения необходимых характеристик для его заключительного использования. Асфальт, идущий на изготовление кровельных материалов, производится воздушной продувкой. Остаток нагревается в трубе почти до температуры вспышки и загружается в колонну продувки, куда горячий воздух нагнетается в течение заданного периода времени. Дегидрирование асфальта образует сероводород, а окисление - двуокись серы. Пар используется для защиты верхней части башни с целью захвата загрязнителей и пропускается через скруббер с целью конденсирования углеводородов. Вакуумная перегонка обычно используется для производства дорожного асфальта. Остаток нагревается и загружается в колонну, где используется вакуум для предотвращения крекинга.
Конденсируемый пар различных процессов производства асфальта будет содержать ничтожные количества углеводородов. Любое нарушение вакуума может привести к поступлению атмосферного воздуха и последующему пожару. При производстве асфальта повышение температуры дна башни вакуумной перегонки с целью улучшения КПД может образовывать метан путем термического крекинга. Это создает пары в резервуарах хранения асфальта, где температуры находятся в диапазоне воспламенения. Воздушная продувка может создавать многоядерные ароматсоединения (то есть полициклические ароматические углеводороды). Конденсируемый пар процесса производства асфальта с помощью воздушной продувки может также содержать различные загрязнители. Очистка углеводородов от активной серы и процессы обработки Многие продукты, такие как термические нафты, полученные в результате легкого крекинга, коксования или термического крекинга, и высокосернистые нафты и дистилляты, полученные в результате перегонки сырой нефти, требуют обработки для использования в смесях бензина и топливных смесях. Продукты перегонки, включая керосин и другие дистилляты, могут содержать ничтожные количества аромосоединений, а нафтены и базовые компоненты смазочных материалов могут содержать воск. Эти нежелательные вещества удаляются либо на промежуточных стадиях нефтепереработки, либо до посылки продуктов на смешивание и хранение путем таких процессов очистки, как извлечение растворителем и депарафинизация растворителем. Ряд промежуточных и конечных продуктов, включая средние дистилляты, бензин, керосин, топливо для реактивных двигателей и сернистые газы, должны быть высушены и очищены от активной серы. Обработка выполняется либо на промежуточной стадии процесса переработки, либо перед посылкой конечных продуктов на смешивание и хранение. Обработка удаляет из нефти загрязняющие вещества, такие как органические соединения, содержащие серу, азот и кислород, растворенные металлы, неорганические соли и растворяемые соли, растворенные в эмульгированной воде. Обрабатывающие материалы - это кислоты, растворители, щелочи и окисляющие и адсорбционные агенты. Обработка кислотой используется для улучшения запаха, цвета и других свойств базовых компонентов смазки для предотвращения коррозии и загрязнения катализатора и для улучшения стабильности продукта. Сероводород, который удаляется из “сухого” сернистого газа с помощью поглощающего агента (диэтиноламина), испаряется, используется как топливо или преобразуется в серу. Тип обработки и тип агентов зависит от базовых компонент сырой нефти, промежуточных процессов и спецификации конечного продукта. Процессы обработки растворителем С помощью растворителей выделяют ароматосоединения, нафтены и примеси из потоков продуктов путем растворения или осаждения. Извлечение растворителем предотвращает коррозию, защищает катализатор в последующих процессах и улучшает конечные продукты путем удаления ненасыщенных, ароматических углеводородов из базовых компонент смазки и смазочного материала.
Исходное сырье высушивается и подвергается непрерывной противоточной обработке растворителем. В одном процессе исходное сырье моется с помощью жидкости, в которой вещества, которые должны быть удалены, лучше растворяются, чем в желанном результирующем продукте. В другом процессе добавляются отобранные растворители, вызывая выпадение примесей в осадок вне продукта. Растворитель отделяется от потока продуктов нагреванием, испарением или фракционированием, при этом ничтожные количества остатка впоследствии удаляются из рафината адсорбцией пара или вакуумной отпаркой. Электрическое осаждение может использоваться для разделения неорганических соединений. Затем растворитель восстанавливается, чтобы снова использоваться в процессе. Типичные химические вещества, используемые в процессе извлечения, включают широкий набор кислот, щелочей и растворителей, включая фенол и фурфурал, а также окисляющие и адсорбционные агенты. В адсорбционном процессе высоко пористые твердые материалы собирают жидкие молекулы на своих поверхностях. Выбор определенных процессов и химических веществ зависит от характера обрабатываемого исходного сырья, присутствующих загрязняющих веществ и требований, предъявляемых к конечному продукту. (См. Рис.78.19) -------------------------------------------------------------------------------- Рис. 78.19 Процесс извлечения растворителем

-------------------------------------------------------------------------------- Депарафинизация растворителем устраняет воск или из дистиллята, или из остаточных базовых компонент, и может применяться на любой стадии процесса нефтепереработки. При депарафинизации растворителем исходное сырье воска охлаждается в теплообменнике и холодильнике, а растворитель добавляется, чтобы помочь сформировать кристаллы, которые удаляются вакуумной фильтрацией. Депарафинизированная нефть и растворитель оплавляются и отпариваются, а воск проходит через водный отстойник, установку для ректификации растворителя и башню оплавления. (См. Рис. 78.20) -------------------------------------------------------------------------------- Рис. 78.20 Процесс депарафинизации растворителем

-------------------------------------------------------------------------------- Деасфальтизация растворителем отделяет тяжелые фракции нефти для производства тяжелых смазочных материалов, исходного сырья для каталитического крекинга и асфальта. Исходное сырье и жидкий пропан (или гексан) перекачиваются к башне извлечения, при этом смеси, температуры и давления точно контролируются. Разделение происходит в замыкателе с вращающимся диском на основе разностей растворимости. Продукты затем испаряются и подвергаются адсорбционной обработке паром для регенерации пропана с целью его последующего рециркулирования. Деасфальтизация растворителем также удаляет серу и соединения азота, металлы, углеродистые остатки и парафины из исходного сырья. (См. Рис. 78.21) -------------------------------------------------------------------------------- Рис. 78.21 Процесс деасфальтизации растворителем
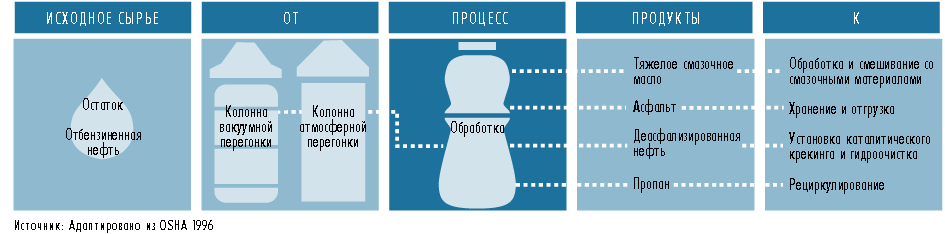
-------------------------------------------------------------------------------- Соображения по поводу здоровья и безопасности При депарафинизации растворителем нарушение вакуума (подсосы воздуха) создает потенциальную опасность пожара и взрыва, позволяя воздуху войти в установку. Существует потенциальная возможность вредного воздействия на персонал депарафинизирующих паров растворителя, смеси метилэтилкетона и толуола. Хотя извлечение растворителем - замкнутый процесс, имеется потенциальная возможность воздействия канцерогенных полициклических ароматических углеводородов, технологического масла и растворителей извлечения, таких как фенол, фурфурал, гликоль, метилэтилкетон, амины и другие химические вещества во время обработки и операций. Деасфальтизация требует точного контроля температуры и давления с целью избежания осадка. Кроме того, влажность, избыточный растворитель или падение рабочей температуры может вызывать пенообразование, которое влияет на контроль над температурой продукта и может создавать осадок. Контакт с горячими нефтяными потоками явиться причиной ожогов кожи. Существует потенциальная возможность воздействий горячих нефтяных потоков, содержащих канцерогенные полициклические ароматические соединения, сжиженный пропан и пары пропана, сероводород и двуокись серы. Процессы гидроочистки Гидроочистка используется для удаления приблизительно 90 % загрязняющих веществ, включая азот, серу, металлы и ненасыщенные углеводороды (олефины) из жидких нефтяных фракций, таких как бензин прямого погона. Гидроочистка подобна гидрокрекингу в том, что и водород и катализатор используется для обогащения водородом исходного сырья олефинов. Однако, степень насыщения не столь велика, как при гидрокрекинге. Обычно, гидроочистка выполняется до начала таких процессов, как каталитический реформинг с тем, чтобы катализатор не был загрязнен необработанным исходным сырьем. Гидроочистка также выполняется перед каталитическим крекингом с целью уменьшения серы и улучшения выхода продукта и для модернизации бензина средней перегонки в очищенный керосин, дизельное топливо и мазуты, используемые для обогрева.
Процессы гидроочистки различаются в зависимости от исходного сырья и катализаторов. Гидродесульфурация удаляет серу из керосина, восстанавливает ароматосоединения, уменьшает характеристики формирования смолы и насыщает олефины. Гидрореформинг - процесс дегидрирования, используемый для восстановления избыточного водорода в производстве высокооктанового бензина. Гидроочищенные продукты смешиваются или используются в качестве исходного сырья для каталитического реформинга. При каталитической гидросульфурации исходное сырье деаэрируется, смешивается с водородом, предварительно нагревается и прокачивается под высоким давлением через реактор с фиксированным катализатором. Водород отделяется и рециркулирует, а продукт стабилизируется в колонне отпаривания, где легкие фракции удаляются. В течение этого процесса соединения серы и азота, представленные в исходном сырье, преобразуются в сероводород ( ) и аммиак ( ). Остаточный сероводород и аммиак удаляются либо адсорбцией паром, комбинированным разделением при высоком и низком давлении или промывкой амином, которая восстанавливает сероводород в высоко сконцентрированном потоке, пригодным для преобразования в элементарную серу. (См. Рис.78.22 и Рис. 78.23) -------------------------------------------------------------------------------- Рис. 78.22 Процесс гидродесульфурации

-------------------------------------------------------------------------------- Рис. 78.23 Схема процесса гидродесульфурации

-------------------------------------------------------------------------------- При гидроочистке содержание сероводорода в исходном сырье должно быть строго сведено до минимума с целью уменьшения коррозии. Хлористый водород может образоваться и конденсироваться как соляная кислота в низкотемпературных частях установки. Гидросульфид аммония может формироваться в высокотемпературных установках высокого давления. В случае выброса существует опасность воздействия паров ароматической компоненты, которая содержит бензол, сероводород, водородный газ или аммиак, если происходит утечка сернистой воды или ее разлив. Фенол может также присутствовать, если обрабатывается исходное сырье с высокой температурой кипения. Чрезмерно большое время контакта и/или температура приводит к коксованию установки. Следует предпринять меры предосторожности при разгрузке катализатора из установки коксования с целью предотвращения возгорания сульфида железа. Такой катализатор должен быть охлажден ниже 49 °C перед удалением, или помещен в бункеры, которые являются инертными по отношению к азоту, где он может быть охлажден перед дальнейшей обработкой. Специальные антипенные добавки могут использоваться для предотвращения отравления катализатора в результате переноса силикона в исходном сырье установки для коксования. Другие процессы очистки от активной серы и обработки Процессы обработки, сушки и очистки от активной серы используется для удаления примесей из компонент смешивания. (См. Рис. 78.24) -------------------------------------------------------------------------------- Рис. 78.24 Процессы очистки от активной серы и обработки

-------------------------------------------------------------------------------- Процессы очистки от активной серы использует воздух или кислород. Если избыток кислорода входит в эти процессы, возможно возникновение пожара в отстойнике вследствие образования статического электричества. Существует потенциальная опасность воздействия сероводорода, двуокиси серы, щелочей (гидрооксид натрия), использованной щелочи, использованного катализатора (Merox), пыли катализатора и агентов очистки от активной серы (углекислый натрий и бикарбонат натрия). Установки амина (обработка кислым газом) Сернистый газ (топливный газ, образующийся в результате таких процессов, как каталитический крекинг и гидроочистка, который содержит сероводород и двуокись углерода) должен обрабатываться до того, как он может быть использован в качестве нефтезаводского топлива. Установки амина удаляют кислотные загрязняющие вещества из потоков сернистого газа и углеводорода. В установках амина газовые и жидкие углеводородные потоки, содержащие двуокись углерода и/или сероводород загружаются в башню газового поглощения или жидкий контактор, где кислотные загрязнители поглощаются текущими в противоположных направлениях растворами амина - моноэтаноламином (MEA), диэтаноламином (DEA) или метилдиэтаноламином (MDEA). Отпаренный газ или жидкость удаляются из верхней части, а амин посылается к регенератору. В регенераторе сернистые компоненты отпариваются под действием тепла и кипячения и удаляются, в то время как амин рециркулирует.
С целью минимизации коррозии должен быть установлен правильный порядок работы, а температуры дна регенератора и кипятильника должны контролироваться. Для предотвращения окисления амина кислород не должен быть допущен в систему. Существует потенциальная возможность вредного воздействия на персонал соединений амина (то есть, MEA, DEA, MDEA), сероводорода и двуокиси углерода. Очистка от активной серы и сушка Очистка от активной серы (удаление меркаптана) осуществляет обработку сернистых соединений (сероводород, тиофен и меркаптан) с целью улучшения цвета, запаха и устойчивости к окислению и уменьшения концентраций двуокиси углерода в бензине. Некоторые меркаптаны удаляются путем обеспечения контакта продукта с растворимыми в воде химическими веществами (например, серная кислота), которые вступают в реакцию с меркаптанами. Щелочная жидкость (гидрооксид натрия), соединения амина (диэтаноламин) или очистка от активной серы с помощью стационарного слоя катализатора может использоваться для преобразования меркаптанов в менее нежелательные дисульфиды. Сушка продукта (удаление воды) выполняется поглощением воды с или без адсорбционных агентов. Некоторые процессы одновременно сушат и очищают от активной серы путем адсорбции на молекулярных ситах. Восстановление серы Восстановление серы удаляет сероводород из потоков сернистых газов и углеводородов. Процесс Клауса (Clause) преобразует сероводород в элементарную серу с помощью термических и каталитических реакций. После сжигания сероводорода при контролируемых условиях газоотделяющие сепараторы удаляют воду и углеводороды из потоков подаваемого газа, которые затем подвергаются воздействию катализатора с целью восстановления дополнительной серы. Серный пар от сжигания и преобразования конденсируется и восстанавливается. Обработка остаточного газа Как окисление, так и восстановление используются для обработки остаточного газа, поступающего из установок восстановления серы, в зависимости от состава газа и экономических условий нефтеперерабатывающего завода. Окислительные процессы сжигают остаточный газ с целью преобразования всех сернистых соединений в двуокись серы, а процессы перегонки преобразуют сернистые соединения в сероводород. Очистка от сероводорода в скруббере Очистка от сероводорода в скруббере - основной процесс обработки исходного сырья углеводородов, используемый для предотвращения отравления катализатора. В зависимости от исходного сырья и характера загрязняющих веществ, методы десульфурации будут меняться от поглощения древесного угля, активированного при температуре окружающей среды, до высокотемпературного каталитического гидрирования, сопровождаемого обработкой окисью цинка. Установки насыщенного и ненасыщенного газа Исходное сырье от различных нефтеперерабатывающих установок посылается к установкам очистки газа, где бутаны и бутены удаляются с целью использования в качестве исходного сырья для алкилирования, более тяжелые компоненты посылаются для смешивания бензина, пропан восстанавливается для сжиженного нефтяного газа, а пропилен удаляется для использования в нефтепродуктах. Установки насыщенного газа отделяют компоненты от нефтезаводских газов, включая бутаны для алкилирования, пентаны для смешивания бензина, сжиженные нефтяные газы для топлива и этан для нефтепродуктов. Имеются два различных процесса для насыщенных газов: поглощение-фракционирование и прямое фракционирование. При поглощении-фракционировании газы и жидкости от различных установок подаются к абсорберу/деэтанизатору, где и более легкие фракции отделяются поглощением регенерированного абсорбционного масла и удаляются для использования в качестве топливного газа или сырья нефтепродуктов. Остающиеся более тяжелые фракции отпариваются и посылаются в дебутанизатор, а регенерированное абсорбционное масло рециркулирует назад к абсорберу/деэтанизатору. отделяется от пентанов в дебутанизаторе, отмывается в скруббере с целью устранения сероводорода и подается к делителю для отделения пропана и бутана. Во фракционирующих колоннах отсутствует стадия поглощения. Процессы насыщенных газов зависят от исходного сырья и требований, предъявляемых к продукту. Коррозия происходит из-за присутствия сероводорода, двуокиси углерода и других соединений, полученных в результате предварительной обработки. Потоки, содержащие аммиак, должны быть высушены перед началом изготовления. Антизагрязняющие добавки используется в поглотительном масле с целью защиты теплообменников. Ингибиторы коррозии используются для управления коррозией в верхних системах. Существует потенциальная опасность воздействия сероводорода, двуокиси углерода, гидрооксида натрия, MEA, DEA и MDEA, которые должны поступить после предварительной обработки. Установки ненасыщенных газов восстанавливают легкие углеводороды из потоков жирного газа, идущего от каталитических крекер-установок и верхних накопителей установки замедленного коксования или приемных резервуаров фракционирования. В типичном процессе жирные газы сжимаются и обрабатываются амином с целью устранения сероводорода либо до, либо после входа во фракционирующий поглотитель, где они смешиваются в одновременном потоке дебутанизированного бензина. Легкие фракции отделяются с помощью тепла в кипятильнике, при этом обработавший газ посылается к губчатому поглотителю, а отстой посылается в бутанизатор. Часть дебутанизированного углеводорода рециркулирует, а баланс идет к делителю для разделения. Верхние газы идут к депропанизатору для использования в качестве исходного сырья установки алкилирования. (См. Рис. 78.25) -------------------------------------------------------------------------------- Рис. 78.25 Процесс установки ненасыщенного газа

-------------------------------------------------------------------------------- Из-за влажного сероводорода и цианидов может иметь место коррозия в установках ненасыщенных газов, которые обрабатывают исходное сырье каталитического крекинга с флюидизированным катализатором. Существует возможность коррозии вследствие воздействия сероводорода и отложений в секциях высокого давления газовых компрессоров от аммиачных соединений, когда исходное сырье поступает от установки замедленного коксования или каталитического крекинга с термофором. Существует потенциальная возможность воздействия сероводорода и таких соединений, как MEA, DEA и MDEA. Процессы смешивания базовых компонент бензина, дистиллятного топлива, смазочного материала Смешивание - физическое смешивание ряда различных жидких углеводородных фракций с целью производства конечных продуктов с определенными желательными характеристиками. Продукты могут быть смешаны в газопроводном потоке при движении по трубопроводам или партиями путем смешивания в резервуарах и сосудах. Смешивание в газопроводе базовых компонент бензина, дистиллятов, топлива для реактивных двигателей и смазочного материала выполняется путем впрыскивания пропорциональных количеств каждого компонента в основной поток, где турбулентность содействует полному смешиванию. · Бензины - смеси продуктов реформинга, алкилатов, бензина прямого погона, термически и каталитически крекированных бензинов, бензина установки коксования, бутана и соответствующих добавок. · Мазут и дизельное топливо - смеси дистиллятов и оборотной нефти, а топливо для реактивных двигателей может быть дистиллятом прямого погона или смешанным с нафтой. · Смазочные материалы - смеси очищенных базовых компонент · Асфальт смешивается из различных остаточных компонент в зависимости от предназначения. Добавки часто добавляются в бензин и моторные топлива во время или после смешивания для обеспечения определенных свойств, несвойственных нефтяным углеводородам. Эти добавки включают средства повышения октанового числа, антидетонационные агенты, антиокислители, ингибиторы смолообразования, ингибиторы пенообразования, ингибиторы коррозии, очистители карбюратора (углерода), детергенты для очистки впрыскивателя, одоризаторы дизеля, цветные красители, антистатик дистиллята, окислители бензина, такие как метанол, этанол и метилтерциарибутилэфир, деактиваторы металла и другие. Операции смешивания партиями и в газопроводе требует строгого контроля для поддержания желаемого качества продукции. Разлитые вещества должны быть очищены, а места утечек починены во избежание подскальзываний и падений. С добавками, содержащимися в барабанах и мешках, следует обращаться должным образом во избежание напряжения и воздействий. Существует потенциальная опасность контакта с опасными добавками, химическими веществами, бензолом и другими материалами во время смешивания, и требуются соответствующие технические контрольные приборы, индивидуальные средства защиты и соблюдение должных мер гигиены для сведения воздействий к минимуму.
Не нашли, что искали? Воспользуйтесь поиском:
|