Главная
Популярная публикация
Научная публикация
Случайная публикация
Обратная связь
ТОР 5 статей:
Методические подходы к анализу финансового состояния предприятия
Проблема периодизации русской литературы ХХ века. Краткая характеристика второй половины ХХ века
Ценовые и неценовые факторы
Характеристика шлифовальных кругов и ее маркировка
Служебные части речи. Предлог. Союз. Частицы
КАТЕГОРИИ:
|
Фотографии установок первичной переработки различной конфигурации 2 страница
-------------------------------------------------------------------------------- Рис. 78.2 Процесс обессоливания (предварительной обработки)

-------------------------------------------------------------------------------- Плохое обессоливание вызывает загрязнение труб нагревателей и теплообменников во всех устройствах нефтепереработки, ограничивая поток продуктов и передачу их тепла, и приводит к разгерметизации оборудования вследствие увеличения давления и температур. Чрезмерное давление в обессоливающем устройстве вызывает выход его из строя. Коррозия, которая имеет место вследствие присутствия сероводорода, хлористого водорода, нафтеновых (органических) кислот и других загрязнителей сырой нефти, также вызывает выход из строя оборудования. Коррозия происходит тогда, когда нейтрализованные соли (хлориды и сульфиды аммония) увлажняются конденсированной водой. Так как обессоливание - закрытый процесс, существует небольшая вероятность воздействия сырой нефти или технических химических веществ на человека, если только не происходит утечка или выброс. Пожар может иметь место в результате утечки в нагревателях, приводящей к выбросу компонента сырой нефти с низкой температурой кипения. Во время обессоливания существует вероятность воздействия аммиака, сухих химических деэмульгаторов, щелочей или кислот. Там, где при обессоливании сернистой сырой нефти используются повышенные температуры, будет присутствовать сероводород. В зависимости от исходного сырья - сырой нефти и используемых при обработке химических веществ, сточные воды будут содержать различные количества хлоридов, сульфидов, бикарбонатов, аммиака, углеводородов, фенола и взвешенных твердых веществ. Если при фильтрации используется инфузорная земля, ее воздействия должны быть сведены к минимуму или должны контролироваться, так как инфузорная земля может содержать кремнозем с частицами очень маленького размера, что делает ее потенциально опасной для органов дыхания. Процессы разделения сырой нефти Первый шаг при переработке нефти - фракционирование сырой нефти в колоннах атмосферной и вакуумной перегонки. Нагретая сырая нефть физически разделяется на различные фракции или фракции прямой перегонки, отличающиеся определенными диапазонами температур кипения и классифицируемые в порядке уменьшения летучести как: газы, легкие дистилляты, средние дистилляты, газойли и остатки. Фракционирование работает, так как градация по температуре от нижней части до верхней части колонны перегонки заставляет компоненты с более высокими температурами кипения конденсироваться первыми, в то время как фракции с более низкими температурами кипения поднимаются выше в колонне прежде, чем они конденсируются. Внутри колонны поднимающиеся пары и опускающиеся жидкости (орошение) смешиваются на уровнях, где их составы находятся в динамическом равновесии друг с другом. На этих уровнях (ректификационных тарелках) располагаются специальные лотки, которые удаляют фракцию жидкости, которая конденсирует на каждом уровне. В типичной двухступенчатой установке по переработке сырой нефти за колонной атмосферной перегонки, производящей легкие фракции и дистилляты, немедленно следует колонна вакуумной перегонки, которая обрабатывает атмосферные остатки. После перегонки только небольшое количество углеводородов подходят для использования в качестве конечного продукта без дальнейшей обработки. Атмосферная перегонка В колоннах атмосферной перегонки опресненное исходное сырье - сырая нефть - предварительно нагревается, используя регенерированное тепло процесса. Оно затем поступает к нагревателю нефти прямой перегонки и после нагрева подается в вертикальную ректификационную колонну прямо над основанием при давлениях, слегка превышающих атмосферное и при температурах от 343°C до 371°C во избежание нежелательного термического крекинга, который происходит при более высоких температурах. Более легкие фракции (низкая температура кипения) проникают в верхнюю часть колонны и непрерывно удаляются и направляются к другим установкам для дальнейшей переработки, обработки, смешивания и распределения.
Фракции с самыми низкими температурами кипения, такие как топливный газ и легкая нафта, удаляются из верхней части колонны по верхней трубе как пары. Нафта или бензин прямого погона берутся из верхней секции колонны как верхний поток. Эти продукты используются в качестве исходного сырья при производстве нефтепродуктов и исходного сырья для реформинг-установки, сырья для смешивания с компонентами бензинов, в качестве растворителей и сжиженных нефтяных газов. Фракции с промежуточным диапазоном кипения, включая газойль, тяжелую нафту и дистилляты, удаляются из средней секции колонны как боковые потоки. Они направляются к конечным операциям для получения керосина, дизельного топлива, мазута, топлива для реактивных двигателей, сырья для каталитических крекинг-установок и компонентов смешивания. Некоторые из этих жидких фракций отпариваются от их более легких фракций, которые возвращаются в колонну в качестве движущихся сверху вниз потоков орошения. Более тяжелые фракции с более высокими температурами кипения (называемые мазутом, отстоем или верхней нефтью), которые конденсируются или остаются на дне колонны, используются для мазута, производства асфальта или исходного сырья для крекинга, или направляются к нагревателю и в колонну вакуумной перегонки для дальнейшего фракционирования. (См. Рис. 78.3 и Рис. 78.4). -------------------------------------------------------------------------------- Рис. 78.3 Процесс атмосферный перегонки
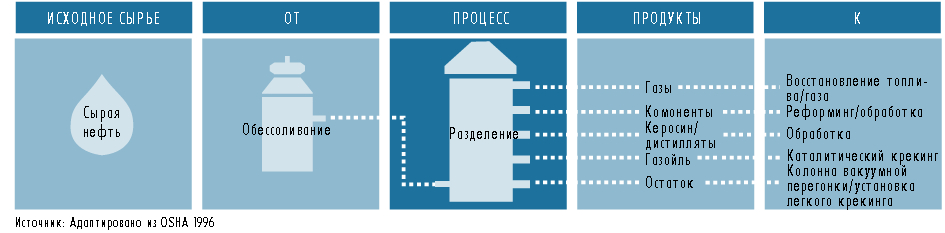
-------------------------------------------------------------------------------- Рис. 78.4 Блок-схема процесса атмосферной перегонки

-------------------------------------------------------------------------------- Вакуумная перегонка Колонны вакуумной перегонки обеспечивают пониженное давление, требуемое для предотвращения термического крекинга при перегонке остатка или верхней сырой нефти из колонны атмосферной перегонки при более высоких температурах. Внутренние конструкции некоторых колонн вакуумной перегонки отличаются от конструкций колонн атмосферной перегонки в том, что вместо лотков используются случайно расположенные насадки и площадки с туманоуловителями. Колонны большего диаметра используются для поддержания скоростей на более низком уровне. Типичная колонна вакуумной перегонки первой стадии может производить газойли, базовые компоненты смазочных масел и тяжелые остатки для деасфальтизации пропаном. Колонна второй стадии, работающая при более низком вакууме, дистиллирует избыточный остаток из колонны атмосферной перегонки, который не используется при изготовлении исходного сырья смазки, и избыточный остаток из первой башни вакуумной перегонки не используется для деасфальтизации. Колонны вакуумной перегонки обычно используются для отделения сырья каталитического крекинга от избыточного остатка. Отстои колонны вакуумной перегонки могут быть также посланы в установку для коксования, использоваться в качестве смазочного материала или сырья для асфальта или быть десульфурированы и смешаны с мазутом с низким содержанием серы. (см. Рис. 78.5 и Рис. 78.6).
-------------------------------------------------------------------------------- Рис. 78.5 Процесс вакуумной перегонки

-------------------------------------------------------------------------------- Рис. 78.6 Схема процесса вакуумной перегонки

-------------------------------------------------------------------------------- Ректификационные колонны На нефтеперерабатывающих заводах имеются другие многочисленные ректификационные колонны меньшего размера, спроектированные для разделения определенных и уникальных продуктов, которые все работают по тому же самому принципу, что и колонны атмосферной перегонки. Например, депропанизатор - маленькая колонна, разработанная для отделения пропана от изобутана и более тяжелых компонентов. Другая колонна большего размера используется для разделения этилбензола и ксилола. Маленькие “пузырьковые” колонны, называемые секциями отпаривания, используют острый пар для удаления небольших количеств легких продуктов (бензина) из более тяжелых нефтепродуктов. Контрольные температуры, давления и орошение должны поддерживаться внутри пределов рабочих параметров для предотвращения термического крекинга внутри ректификационных колонн. Предусматривается использование систем аварийного сброса, так как могут иметь место отклонения давления, температур или уровней жидкости, при выходе из строя приборов автоматического контроля. Исходное сырье - сырая нефть может содержать значительные количества воды во взвешенном состоянии, которая отделяется во время пуска, и вместе с водой, остающейся в колонне после продувки паром, осаждается на дне колонны. Эта вода может нагреваться до температуры кипения и создавать мгновенный паровой взрыв после контакта с нефтью, находящейся в установке. Теплообменники предварительного подогрева, печь и теплообменник отстоя, колонна атмосферной перегонки и вакуумная печь, колонна вакуумной перегонки и ее верхняя часть - восприимчивы к коррозии со стороны соляной кислоты (HCl), сероводорода ( ), воды, сернистых соединений и органических кислот. При обработке сернистой сырой нефти может иметь место сильная коррозия как в колоннах атмосферной, так и вакуумной перегонки, где температуры металлов превышают 232°C, и в трубах печи. Сероводород ( ) также вызывает трещины в стали. При обработке сырой нефти с высоким содержанием азота, окиси азота, которые являются коррозионными по отношению к стали, образуются в топочных газах печей при охлаждении их до низких температур в присутствии воды. Химические вещества используются для контроля коррозионного действия соляной кислоты на оборудование ректификационных установок. Аммиак может быть введен в верхний поток колонны до начала конденсации паров и/или щелочной раствор может быть осторожно введен в горячее сырье сырой нефти. Если не вводится достаточного количества воды для промывки нефти на стадии обессоливания, могут образовываться отложения хлорида аммония, вызывая сильную коррозию.
Атмосферная и вакуумная перегонка - закрытые процессы, и воздействия при них на человека являются минимальными. Когда обрабатывается кислая (высокосернистая) нефть, могут существовать потенциальные возможности воздействия сероводорода в теплообменнике предварительного нагрева и печи, зоне ввода сырья в колонну и верхней системе, вакуумной печи и колонне, теплообменнике отстоя. Вся сырая нефть и продукты перегонки содержат ароматические соединения с высокой температурой кипения, включая канцерогенные полициклические ароматические углеводороды. Краткосрочные воздействия высоких концентраций паров нефти могут привести к головным болям, тошноте и головокружению, а длительное воздействие может привести к потере сознания. Бензол присутствует в ароматической нафте, и его воздействие на персонал должно быть ограничено. Верхняя гексаноотгонная колонна может содержать большие количества обычного гексана, который может воздействовать на нервную систему. Хлористый водород может присутствовать в теплообменнике предварительного нагрева, верхних зонах колонны. Сточные воды могут содержать растворимые в воде сульфиды высокой концентрации и другие, растворимые в воде соединения, такие как аммиак, хлориды, фенол и меркаптан, в зависимости от исходного сырья сырой нефти и химических веществ обработки. Процессы преобразования сырой нефти Процессы преобразования, такие как крекинг, объединение и перегруппирование, изменяют размер и структуру молекул углеводорода с тем, чтобы преобразовать фракции в более желанные продукты. (См. Таблицу 78.3). --------------------------------------------------------------------------------
Таблица 78.3 Краткий обзор процессов переработки нефти
Название процесса
| Действие
| Метод
| Цель
| Исходное сырье
| Изделия
| Процессы фракционирования
| Атмосферная перегонка
| Разделение
| Термический
| Разделить фракции
| Опресненная сырая нефть
| Газ, газойль, дистиллят, остаток
| Вакуумная перегонка
| Разделение
| Термический
| Разделить без расщепления
| Остаток колонны атмосферной перегонки
| Газойль, масляный дистиллят, остаток
| Процессы преобразования - Разложение
| Каталитический крекинг
| Изменение
| Каталитический
| Усовершенствовать бензин
| Газойль, дистиллят кокса
| Бензин, исходное сырье нефтепродуктов
| Коксование
| Полимеризация
| Термический
| Преобразовать вакуумные остатки
| Остаток, тяжелая нефть, гудрон
| Нафта, газойль, кокс
| Гидрокрекинг
| Гидрирование
| Каталитический
| Преобразовать в более легкие углеводороды
| Газойль, крекированная нефть, остатки
| Более легкие и более высококачественные продукты
| Паровой реформинг водорода
| Разложение
| Термический/ каталитический
| Произвести водород
| Десульфированный газ, , пар
| Водород, СО,
| Паровой крекинг
| Разложение
| Термический
| Расщепить большие молекулы
| Тяжелое топливо/дистиллят колонны атмосферной перегонки
| Крекированная нафта, кокс, остатки
| Легкий крекинг
| Разложение
| Термический
| Уменьшить вязкость
| Остаток колонны атмосферной перегонки
| Дистиллят, крекинг-остаток
| Процессы преобразования - Объединение
| Алкилирование
| Комбинирование
| Каталитический
| Объединить олефины и изопарафины
| Изобутан /олефины крекинг-установки
| Изооктан (алкилат)
| Приготовление консистентной смазки
| Комбинирование
| Термический
| Совместить мыла и масла
| Смазочное масло, жирная кислота
| Консистентная смазка
| Полимеризация
| Полимеризация
| Каталитический
| Объединить два или более олефинов
| Олефины крекинг-установки
| Высокооктановая нафта, компоненты нефтепродуктов
| Процессы преобразования- Изменение/перегруппирование
| Каталитический реформинг
| Изменение/ дегидирование
| Каталитический
| Усовершенствовать низкооктановую нафту
| Нафта установки коксования/гидрокрекинг-установки
| Высокооктановый продукт реформинга/аромат-соединение
| Изомеризация
| Перегруппирование
| Каталитический
| Преобразовать прямую цепочку углеводородов в разветвленную
| Бутан, пентан, гексан
| Изобутан/пентан/гексан
| Процессы обработки (очистки)
| Очистка амином
| Обработка
| Поглощение
| Удалить кислотные загрязнители
| Сернистый газ, углеводороды с
и
| Бескислотные газы и жидкие углеводороды
| Обессоливание (предварительная очистка)
| Дегидратация
| Поглощение
| Удалить загрязнители
| Сырая нефть
| Опресненная сырая нефть
| Сушка и очистка от активной серы
| Обработка
| Поглощение / термический
| Удалить и сернистые соединения
| Жидкий углеводород, сжиженный нефтяной газ, алкилированное исходное сырье
| Очищенные от серы и сухие углеводороды
| Извлечение фурфуролом
| Извлечение растворителем
| Поглощение
| Усовершенствовать средний дистиллят и масла
| Оборотный газойль и исходное сырье масел
| Высококачественный дизель и смазочное масло
| Гидродесульфурация
| Обработка
| Каталитический
| Удалить серу, загрязнители
| Высокосернистый остаток/газойль
| Десульфурированные олефины
| Гидрочистка
| Гидрирование
| Каталитический
| Удалить примеси/насыщенные углеводороды
| Остатки, углеводороды крекинга
| Сырье крекинг-установки, дистиллят, смазочное масло
| Извлечение фенолом
| Извлечение растворителем
| Поглощение/ термический
| Улучшить показатель вязкости масел, цвет
| Базовые компоненты масляного сырья
| Высококачественное смазочное масло
| Деасфальтизация растворителем
| Обработка
| Поглощение
| Удалить асфальт
| Остаток колонны вакуумной перегонки, пропан
| Тяжелый компонент смазочного масла, асфальт
| Депарафинизация растворителем
| Обработка
| Охлаждение/ фильтр
| Удалить воск из смазочного масла
| Смазочное масло башни вакуумной перегонки
| Депарафинизированные базовые компоненты смазки
| Извлечение растворителем
| Извлечение растворителем
| Поглощение/ осаждение
| Отделить ненасыщенные ароматсоединения
| Газойль, продукт реформинга, дистиллят
| Высокооктановый бензин
| Очистка от активной серы
| Обработка
| Каталитический
| Удалить преобразовать меркаптан
| Неочищенный дистиллят/бензин
| Высококачественный дистиллят/бензин
|
-------------------------------------------------------------------------------- Ряд углеводородных молекул, которые обычно не присутствуют в сырой нефти, но важны для процесса нефтепереработки, образуются в результате преобразования. Олефины (алкены, диолефины и алкины) - ненасыщенные цепе- или кольцеобразные углеводородные молекулы с, по крайней мере, одной двойной связью. Они обычно образуются путем термического и каталитического крекинга и редко встречаются в необработанной, сырой нефти. Алкены - молекулы с прямой цепочкой, имеющие формулу , содержащие, по крайней мере, одну двойную (ненасыщенную) связь в цепи. Самая простая молекула алкена - моноолефинэтилена с двумя атомами углерода, соединенными двойной связью и четырьмя атомами водорода. Диолефины (содержащие две двойные связи), такие как 1,2-бутадиен и 1,3-бутадиен, и алкины (содержащие тройную связь), такие как ацетилен, встречаются в и более легких фракциях, полученных в результате крекинга. Олефины являются более химически активными, чем парафины или нафтены, и легко объединяется с другими элементами, такими как водород, хлор и бром.
Процессы крекинга После перегонки используются последующие процессы нефтепереработки с целью изменения молекулярных структур фракций с целью создания более желанных продуктов. Один из этих процессов, крекинг, нарушает (или расщепляет) более тяжелые и с более высокой температурой кипения нефтяные фракции на более ценные продукты, такие как газообразные углеводороды, бензин, компоненты смешения бензина, газойль и мазут. Во время этого процесса некоторые молекулы объединяются (полимеризируются) с целью формирования молекулы большего размера. Основные типы крекинга - термический крекинг, каталитический крекинг и гидрокрекинг. Процессы термического крекинга Процессы термического крекинга, разработанные в 1913 году, связаны с нагревом дистиллятных топлив тяжелой нефти под давлением в больших барабанах до тех, пока они не расщепляются в меньшие молекулы с лучшими антидетонационными характеристиками. Этот ранний метод, который был связан с образование большого количества твердого, нежелательного кокса, эволюционировал в современные процессы термического крекинга, включая легкий крекинг, паровой крекинг и коксование. Легкий крекинг Легкий крекинг - мягкая форма термического крекинга, которая уменьшает температуру текучести парафиновых остатков и значительно понижает вязкость компонента без воздействия на диапазон температур кипения. Остатки из колонны атмосферной перегонки мягко растрескиваются в нагревателе при атмосферном давлении. Они затем охлаждаются холодным газойлем для предотвращения чрезмерно глубокого крекинга и испаряются в колонне перегонки. Термически крекированный оставшийся гудрон, который скапливается на дне колонны фракционирования, стабилизируется в вакууме в секции отпаривания, а дистиллят рециркулирует. (См. Рис. 78.7) -------------------------------------------------------------------------------- Рис. 78.7 Процесс легкого крекинга

-------------------------------------------------------------------------------- Паровой крекинг Паровой крекинг производит олефины путем термического крекинга исходных материалов больших углеводородных молекул при давлениях, которые слегка превышают атмосферные и при очень высоких температурах. Остаток парового крекинга смешивается с тяжелым топливом. Нафта, полученная в результате парового крекинга, обычно содержит бензол, который извлекается до гидроочистки. Коксование Коксование - сильная форма термического крекинга, используемая для получения бензина прямого погона (нефть установки коксования) и различных фракций среднего дистиллята, используемых в качестве исходного сырья каталитического крекинга. Этот процесс так полно восстанавливает водород из углеводородной молекулы, что остаток является формой почти чистого углерода, названного коксом. Два наиболее типичных процесса коксования - замедленное коксование и непрерывное (контактное или жидкое) коксование, которые, в зависимости от механизма реакции, времени, температуры и исходного сырья, производят три типа кокса - губчатый, пористый и игольчатый кокс. (См. Рис. 78.8).
-------------------------------------------------------------------------------- Рис. 78.8 Процесс коксования

-------------------------------------------------------------------------------- · Замедленное коксование. При замедленном коксовании исходное сырье сначала загружается во фракционирующую колонну для отделения более легких углеводородов, а затем объединяется с тяжелой оборотной нефтью. Тяжелое исходное сырье подается в коксовую печь и нагревается до высоких температур при низком давлении с целью предотвращения преждевременного коксования в трубах нагревателя, производя частичное выпаривание и мягкий крекинг. Смесь жидкости/пара откачивается из нагревателя к одному или большему числу барабанов установок для коксования, где горячий материал находиться приблизительно 24 часа (замедление) при низком давлении до тех пор, пока он не расщепляется на более легкие продукты. После того как кокс достигает заранее определенного уровня в одном барабане, поток ответвляется к другому барабану для сохранения непрерывного процесса. Пары из барабанов возвращаются в установку фракционирования для разделения газа, нафты и газойлей и для рециркулирования более тяжелых углеводородов через печь. Полный барабан стерилизуется водяным паром для отпаривания некрекированных углеводородов, охлаждается посредством вбрызгивания воды и механически очищается от нагара с помощью сверла, поднимающегося со дна барабана, или гидравлическим путем разрыва пласта кокса с помощью воды высокого давления, выброшенной от вращающегося резца. · Непрерывное коксование. Непрерывное (контактное или жидкое) коксование - процесс с движущимся слоем, который функционирует при более низких давлениях и более высоких температурах, чем замедленное коксование. При непрерывном коксовании происходит термический крекинг путем использования тепла, передаваемого от частиц горячего оборотного кокса к исходному сырью в радиальном смесителе, называемом реактором. Газы и пары берутся из реактора, охлаждаются с целью остановки дальнейшей реакции и фракционируются. После реактора кокс входит в барабан и поднимается к подающему устройству и сортировщику, где большие частицы кокса удаляются. Оставшийся кокс спускается в подогреватель реактора для рециркулирования вместе с исходным сырьем. Процесс является автоматическим в том смысле, что имеется непрерывный поток кокса и исходного сырья, а коксование происходит как в реакторе, так и в барабане. Соображения по поводу здоровья и безопасности При коксовании температурный контроль должен проводиться внутри определенного диапазона, так как при высоких температурах будет образовываться кокс, который является слишком твердым, чтобы его можно было вырезать из барабана. Наоборот, температуры, которые являются слишком низкими, приведут к суспензии твердых частиц в жидкости с высоким содержанием асфальта. Если температуры коксования выходят из-под контроля, может иметь место экзотермическая реакция. При термическом крекинге, когда обрабатываются сернистая нефть, может иметь место коррозия там, где температуры металлов находятся между 232°C и 482°C. Оказывается, что кокс формирует защитный слой на металле при температуре свыше 482°C. Однако, сероводородная коррозия имеет место, когда температуры не контролируются должным образом выше 482°C. Нижняя часть колонны, высокотемпературные теплообменники, печь и барабаны, предназначенные для пропитки, подвергаются коррозии. Непрерывный теплообмен приводит к вспучиванию и растрескиванию оболочек коксовых барабанов.
Водное или паровое впрыскивание используется для предотвращения нарастания кокса в трубах печей установки в случае замедленного коксования. Вода должна полностью вытечь из установки для коксования, чтобы не вызвать взрыв при перезагрузке горячего кокса. В аварийных ситуациях требуются дополнительные средства выхода с рабочей платформы, находящейся наверху кокосовых барабанов. При обращении с горячим коксом могут быть получены ожоги вследствие воздействия пара при утечках из труб или горячей воды, горячего кокса или горячей суспензии твердых частиц, которая может быть выброшена при открытии установок для коксования. Существует потенциальная опасность воздействия ароматической нефти, содержащей бензол, сероводород и угарный газ, и ничтожных количеств канцерогенных полициклических ароматических углеводородов, связанных с операциями коксования. Отходы сернистой воды могут быть высокощелочными и содержать нефть, сульфиды, аммиак и фенол. Когда кокс движется как суспензия твердых частиц, может произойти истощение кислорода внутри замкнутых пространств, таких как бункеры, потому что влажный углерод поглощает кислород. Процессы каталитического крекинга Каталитический крекинг расщепляет сложные углеводороды на более простые молекулы с целью увеличения качества и количества более легких, более желанных продуктов и уменьшения остатков. Тяжелые углеводороды подвергаются действию катализаторов при высокой температуре и низком давлении, которые содействуют химическим реакциям. Этот процесс перегруппировывает молекулярную структуру, преобразуя компоненты тяжелых углеводородов в более легкие фракции, такие как керосин, бензин, сжиженный нефтяной газ, масло и исходное сырье для получения нефтепродуктов (см. Рис. 78.9 и Рис. 78.10). Выбор катализатора зависит от комбинации самой большой возможной реактивности и лучшего сопротивления трению. Катализаторы, используемые в крекинге при нефтепереработке, являются обычно твердыми материалами (цеолит, гидросиликат алюминия, обрабатываемая бентонитная глина, земля Фуллера, боксит и алюминсиликат), которые присутствуют в форме порошков, шариков, гранул или формообразных материалов, называемых штамповками (экструдитами). --------------------------------------------------------------------------------
Не нашли, что искали? Воспользуйтесь поиском:
|