Производство и отгрузка обожженных окатышей 25
2 Расчёт шихты для производства окатышей 31
2.1 Определение расхода концентрата и известняка 36
2.2 Расчет количества компонентов, вносимых сухой шихтой 40
2.3 Определение состава обожженных окатышей 42
3 Специальная часть??????????????? 48
3.1Лабораторные испытания производства железорудных окатышейиз смеси магнетитового концентрата и богатой руды 48
3.2 Автоматизация 59
4 Опробование и контроль технологического процесса 60
4.1 Контроль технологического процесса 60
4.2 Отбор и разделка проб 65
5 Экономика и организация работы производственного подразделения
5.1 Организация производства
5.2 Экономика производственного подразделения 68
6 Безопасность проектных решений 77
6.1 Правила безопасности при размещении оборудования 77
6.2 Промышленная санитария 81
6.3 Охрана окружающей среды 86
6.4 Противопожарные требования при проектировании 88
Заключение 91
Список литературы 92
Приложение
Введение
Михайловский горно-обогатительный комбинат – это крупное предприятие, имеющее сложную структуру. Михайловский ГОК построен на базе Михайловского железорудного месторождения, расположенного в 100 километрах севернее города Курска. Руда залегает мощным пластом шириной до 2,5 км и протяженностью около 7 км. Объем разведанных запасов – более 11 миллиардов тонн.
По объемам производства железорудного сырья для черной металлургии Михайловский ГОК занимает лидирующие позиции в России. Комбинат входит в число предприятий, составляющих основной промышленный потенциал страны. Предприятие активно осваивает богатую сырьевую базу, имеет высокий уровень развития производства. Ежегодно увеличиваются инвестиции в его модернизацию, разрабатываются и внедряются новые энергосберегающие технологии, улучшается качество продукции.
На Михайловском ГОКе осуществляется инвестиционная программа по техническому перевооружению на 350 мил. руб. для этого: проведена широкая реконструкция основного производства на всех этапах технологической цепочки, модернизация горно-транспортной схемы, введена новая линия технологического контроля. Реализация этих проектов позволила увеличить производственные мощности и, что особенно важно, снизить издержки. Комбинат давно отошел от проектных показателей, которые были заложены при строительстве. В прошлом году производство концентрата на комбинате выросло на 31,4% при общем приросте производства железорудной продукции на 57,7%.
Актуальность темы:
Промышленное обследование технологических и теплоэнергетических показателей работы участка шихтоподготовки, анализ фактического состояния оборудования и условий его эксплуатации выявило следующие недостатки, являющиеся причинами - повышенных расходов энергоносителей и недостаточной эффективности работы теплового агрегата.
Цель проекта:
Спроектировать участок шихтоподготовки ФОК ОАО «МГОК» производительностью 14,5 млн тонн офлюсованных окатышей в год со следующими показателями: Содержание FeO в обожженных окатышах 1.15%, основностью 0.20%, степень выгорания серы 69%, расход бентонита на 100 кг окатышей 0,535 кг/т.
Задачи проекта:
· В общей части проекта на основе технологии производства офлюсованных железорудных окатышей сделать выбор, обоснование технологии производства окатышей объёмом 14,5 млн. тонн в год, подбор технологической схемы производства окатышей.
· В расчетной части произвести расчет шихты для производства окатышей.
· В специальной части решить вопрос лабораторных испытаний, отработки технологии производства железорудных окатышейиз смеси магнетитового концентрата и богатой руды
· В разделе контроль и опробование технологических процессов привести карту опробования фабрики окомкования, раскрыть технологию производства железорудных офлюсованных окатышей, перечислить требования к шихтовым материалам и технические требования к обожженным окатышам.
· В разделе организация производства описать структуру управления участка и форму организации труда в проектируемом участке.
· В разделе экономики производства произвести расчет затрат на амортизацию оборудования.
· В разделе безопасность проектных решений предложить схему мероприятий к охране окружающей среды и промышленной санитарии с учетом правил безопасности размещения оборудования и противопожарных требований.
· В графической части провести анализ существующих проектных решений и составить схему цепи аппаратов для участка шихтоподготовки и схему пневмотранспорта для транспортировки известняка и бентонита в силоса корпуса окомкования.
1 Общая часть
Фабрика окомкования МГОКа производит неофлюсованные железорудные окатыши из магнетитового концентрата мокрой магнитной сепарации, и офлюсованные железорудные окатыши из магнетитового концентрата дообогащенного методом флотации. Железорудные окатыши предназначены для использования в качестве исходного сырья в металлургическом переделе.
Технология производства неофлюсованных и офлюсованных окатышей определена требованиями металлургического передела: физико-механическими свойствами, химическим составом. Для получения железорудных неофлюсованных и офлюсованных окатышей на фабрике окомкования используют шихтовые материалы: концентрат железорудный магнетитовый отделения обогащения ДОК, концентрат железорудный магнетитовый отделения флотации ДОК, известняк и бентонит. Обеспечение фабрики исходным сырьем осуществляется:
Концентрат магнетитовый и магнетитовый дообогащенный подается с обогатительной фабрики конвейерным транспортом в расходные бункера фабрики окомкования.
Концентрат офлюсованный подается с ДОК по следующим схемам:
· при производстве одного вида продукции прием офлюсованного концентрата осуществляется по конвейеру ОК-2 со склада ДОК грейферным краном отдельно от магнетитового концентрата в подготовленный бункер, дозирование производится технологическим персоналом ФОК в зависимости от массового содержания железа общего и влаги в подаваемом магнетитовом концентрате.
· при производстве одновременно офлюсованных и неофлюсованных окатышей прием офлюсованного концентрата осуществляется в потоке с магнетитовым концентратом. Отгружается офлюсованный концентрат со склада ДОК грейферным краном не более 3-х ковшей в 1 час.
· Известняк доставляется на фабрику окомкования железнодорожным транспортом.
· Бентонит доставляется на фабрику окомкования железнодорожным транспортом.
Фабрика окомкования является самостоятельным структурным подразделением комбината и включает следующие основные корпуса.
· Корпус вагоноопрокидывателя;
· Склад известняка и бентонита;
· Корпус дробления известняка;
· Корпус дробления и сушки бентонита;
· Корпус измельчения известняка и бентонита;
· Корпус окомкования;
· Корпус обжига с отделением тягодутьевых средств;
· Корпус грохочения;
· Корпус обезвоживания;
· Погрузочный бункер;
· Склады окатышей.
Управление технологией производства окатышей осуществляется инженерно-техническим и технологическим персоналом фабрики в соответствии с требованиями технологической инструкции, режимной картой производства окатышей, внутренними техническими условиями. Контроль над соблюдением технологической инструкции возлагается на главного инженера фабрики, контроль качества продукции возлагается на начальника участка ОТК. Мониторинг технологического процесса фабрики окомкования и условий получения качественных показателей продукции осуществляет ЦТЛ.
1.1Технология приема и подготовки основных компонентов
Технология приема сырья
На фабрике окомкования используют флюсующие добавки в виде известняка, и связующие добавки в виде бентонита, которые поступают на фабрику в вагонах. Прием известняка и бентонита осуществляется согласно стандартам предприятия СТО 06.02, который устанавливает порядок приемки материалов по количеству и качеству. Известняк и бентонит принимают партиями. Партией считают количество известняка или бентонита одной марки, сорта, оформленные одним документом. Прием известняка и бентонита по качеству производит ОТК. Прием известняка и бентонита по количеству ведется путем перевески груженых вагонов на железнодорожных весах в присутствии представителя фабрики. После приемки вагоны с известняком или бентоглиной подаются по 19 железнодорожному пути в корпус вагоноопрокидывателя, где производится их разгрузка с помощью вагоноопрокидывателя ВРС-125. Известняк, крупностью +8-25мм в летний период и +20-70 в зимний период, разгружается в приемный бункер емкостью 546 м3. Материал пластинчатым питателем подается на конвейера ПУ-1-1; СИ-1. Далее перегрузочной самоходной тележкой ТПС-1600-1.2 выгружается на склад (емкостью 12 тыс.т).
Поступающая бентоглина, крупностью 0-100мм и с влажностью, не превышающей 30%, разгружается по той же технологической схеме, что и известняк. Предусмотрен прием бентонита с помощью самоходной тележки ТПС-1600-1,2 непосредственно в корпус сушки на конвейер У-1, далее в дробилку СМД-102, где дробится до крупности 0-20мм и посредством конвейера У-2, подается в приемный склад (закром), емкостью 2,5 тыс. т
Железорудный концентрат на ФОК подается конвейерным транспортом со склада ДОК или непосредственно с технологических секций ДОК. Контроль над количеством и качеством концентрата осуществляется на конвейерах ОК-1 и ОК-2. Количество концентрата определяется путем взвешивания на ленточных весах «Миллитроникс». Контроль качества осуществляется путем отбора проб автоматическим пробоотборником с последующей разделкой проб в ОТК и выполнением соответствующих анализов качества концентрата в ЦТЛ, контроль влажности концентрата производится влагоплотномерами ВПН-03.
Технология производства продукции
Технологическая схема получения окатышей (схема 1.1)
Технологический процесс производства окатышей включает в себя выполнение следующих операций.
· подготовка компонентов шихты;
· дозирование компонентов шихты;
· смешивание компонентов шихты;
· окомкование шихты;
· грохочение сырых окатышей;
· загрузка сырых окатышей на обжиговую машину;
· термообработка окатышей;
· выделение постели и укладка её на тележки обжиговой машины;
Подготовка компонентов шихты
Подготовка известняка включает операции дробления и измельчения с подсушкой, бентонита- дробления (при необходимости), сушки и измельчения с подсушкой. Известняк для дробления подается со склада из штабеля. Выбор известняка со штабеля производится экскаватором ЭВГ-4И или погрузчиком вдоль всей длины штабеля на конвейер КД-1, далее ленточными конвейерами-питателями КД-2 и КД-3 известняк направляется на дробление в молотковые реверсивные дробилки ДМРЭ 14,5×1300 (2шт.).
Регулировка загрузки в молотковые дробилки №1 и №2 производится при помощи шиберов конвейера КД-1. На конвейере КД-1 установлен металлоискатель. Известняк дробится до крупности 0-10мм. Регулировка крупности дробления производится передвижением колосниковых решеток дробилок. После дробления известняк разгружается на конвейер КД-4 и подается в корпус измельчения конвейерами И-1 и И-2. На конвейере И-2 установлена разгрузочная тележка, распределяющая дробленый известняк по 9 расходным бункерам мельничных систем, емкостью 93 м3 каждый.
Бентоглина со склада при помощи экскаватора, погрузчика и самосвала завозится в закром корпуса сушки, с закрома бентоглина подаётся грейферным краном через дозирующее устройство (бункер, конвейер У-3) в сушильный барабан. Из сушильного барабана бентоглина влажностью 15-18% направляется конвейером ПУ-3-1 в аккумулирующий бункер, рассчитанный на 1 час непрерывной работы барабана и далее системой конвейеров ПУ-3-2, ПУ-3-1, И-1, И-2 подается в расходные бункера корпуса измельчения.
В корпусе измельчения установлены три технологические системы №1, №2 и №3 сухого помола с замкнутым вентилируемым циклом и одновременной подсушкой измельчаемых материалов. Мельница №1 и №2 предназначена для подготовки бентонита, мельница №2 и №3- для подготовки известняка (одна рабочая, одна резервная).
В установку для измельчения известняка и бентонита входит:
· Шаровая мельница Ш-50А;
· Мельничный вентилятор ВМ-180-1100
· Топочный агрегат для получения сушильного агента;
· Дозирующие устройства;
· Сепаратор СПЦ 5500-2000;
· Вентиляторы ВВД-11, ВВД-8 (для производства сушильного агента);
· Пылевые циклоны для газоочистки: 1 стадия - Д2350 мм 2 батареи по 2 шт.; 2 стадия - Д1250мм 4 батареи по 3 шт.; 3 стадия- электрофильтры типа УГ2-3-26 и ЭБГМ12-7,5-4-3;
· Дымосос Д-15,5;
· Аэрожелоб;
Система пневмотранспорта из бункеров готовой продукции в силоса корпуса окомкования (камерный пневматический насос ТА-29А).
Дробленый известняк или бентонит с помощью дозирующих устройств системой конвейеров И-3, И-4, И-5, И-6, И-7, И-8, И-9 равномерно загружается в шаровую мельницу. Измельчение ведется до крупности 90% класса - 0,074 мм, и влажности: известняк- 0,4%; бентонит- 7,5-9,0%. Готовый продукт улавливается системой пылеосадительных циклонов, собирается в бункера готовой продукции, откуда камерными насосами через систему трубопроводов пневмотранспорта подается в накопительные силоса корпуса окомкования емкостью 315м3 каждый (два силоса для известняка, два – для бентопорошка). Отработанный воздух мельничных систем выбрасывается в атмосферу после очистки в электрофильтре. Для сушки известняка и бентоглины в загрузочную течку мельницы подается горячий газ, генерируемый в специальном топочном агрегате, который включает:
Топочную камеру, где сжигается природный газ с помощью двух турбулентных горелок. Для исключения возможности образования высокой температуры и поддерживании ее на уровне 1000°С со стороны фронта топки вводится мелкими струями вторичный воздух;
Смесительную камеру, в которую подается воздух для смешивания и снижения температуры сушильного агента до 600°C для известняка, до 450°C для бентоглины. Полученный сушильный агент поступает в мельницу.
Природный газ подается в корпус измельчения из общей магистрали с давлением 0,03 МПа (0,3 кгс/см2). На вводе в корпус установлен регулятор давления РДУК2Н-100/70 для снижения давления до 0,006 МПа, (0,06 кгс/см2). Максимальный расход газа на агрегат составляет 600 нм3/ч.
1.2 Производство сырых окатышей.
Окомкование - это процесс окускования увлажнённых тонко измельчённых материалов, основанный на способности их при перекатывании образовывать гранулы сферической формы (окатыши) без применения непосредственного давления.
Окомкование концентрата, с применением флюсующей (известняк) и упрочняющей (бентонит) добавок, осуществляется в корпусе окомкования (На ФОКе МГОКа на 14 технологических линиях).
И включает в себя следующие технологические операции: дозирование компонентов шихты, смешивание компонентов шихты, окомкование, грохочение.
Известняк и бентонит подаются пневмотранспортом из корпуса измельчения известняка в силоса корпуса окомкования, откуда пневмотранспортом распределяется по 14-ти (для каждого материала) расходным бункером ёмкостью: для известняка – 32,4 м3, для бентонита – 28,4 м3.
В корпус окомкования концентрат подаётся конвейерным транспортом с обогатительной фабрики и распределяется по 28 -ми бункерам ёмкостью 41,3 м3 каждый (по два бункера на одну технологическую линию).
Дозирование компонентов шихты.
Основная задача данной технологической операции заключается в правильном и точном дозировании компонентов шихты. Правильность дозирования обеспечивается расчётом шихты, а точность дозирования – работой основного технологического оборудования.
Известняк используется как флюсующая добавка. Степень офлюсования окатышей определяется отношением (СаО+МgО):SiO2.
Контроль качества дозирования материалов производится непрерывно по показаниям весодозирующего устройства, а корректировка производится на основе данных химических анализов, поступающих шихтовых материалов и обожженных окатышей.
Для получения окатышей с заданной основностью расход известняка, в расчёте на определённое количество концентрата, определяется по уравнению:
(1.1)
где: gи – расход известняка, % от массы концентрата;
(CaO)и,б- массовая доля CaO в известняке и бентоните, %;
В – модуль основности;
(CaO+MgO)к – сумма основных окислов в концентрате (равная 0,45 % для магнетитового концентрата, 0,35 % для флотоконцентрата), %;
SiO2к, SiO2и, SiO2б – массовая доля диоксида кремния в концентрате, известняке и бентоните,%;
gБ – расход бентонита, % от массы концентрата.
Дозировка компонентов шихты - весовая, автоматическая индивидуальная для каждого окомкователя. Дозирование осуществляется в последовательности - концентрат, известняк, бентонит на конвейере ленточного типа ОК – Х – 1 с помощью дозаторов ленточного типа:
для концентрата ДАМ – 141, для известняка ДАВ – 103, для бентонита – ДАВ –0,87. Количество известняка и бентонита, подаваемое в шихту, регулируется автоматически от количества подаваемого концентрата.
Смешивание компонентов шихты.
Смешивание производится с целью получения однородной по химическому и физическому составу шихты и осуществляется индивидуально для каждого окомкователя в шнековых смесителях СШ – 850 ×5600.
Шихтовые материалы подаются в смеситель конвейером, откуда усреднённая шихта системой конвейеров транспортируется в окомкователь.
Окомкование шихты.
Окускование осуществляется в барабанных окомкователях размером 3,6 × 14 метров. Для загрузки каждой из обжиговых машин установлено по семь окомкователей. Окомкование шихты происходит при наличии мелкой фракции окатышей (циркуляционная нагрузка). Наиболее рациональный режим ведения окомкования - режим переката. Оптимальная влажность шихты, обеспечивающая наилучшие показатели процесса грануляции, находится в пределах 9,5 ÷ 9,7 % в зависимости от удельной поверхности концентрата.
Для получения сырых окатышей однородных по физико-химическим свойствам и гранулометрическому составу, обеспечивающих нормальный процесс обжига, необходимо:
· стабильное качество компонентов шихты по физико-химическим свойствам, отвечающее техническим условиям;
· равномерное распределение известняка и бентонита по всей массе шихты (однородность);
· стабильная нагрузка на окомкователи;
· соблюдение технологических параметров производства сырых окатышей.
Нарушение процесса окомкования может произойти в результате отклонения влажности шихты от её оптимального значения и при изменении крупности шихты и удельной поверхности.
Влажность шихты может быть ниже или выше оптимального значения.
Грохочение сырых окатышей.
Операция грохочения сырых окатышей имеет цель классификации сырых окатышей на кондиционные и на некондиционные. Грохочение производится на роликовом грохоте или на инерционном типа ГСТ71 М – СО, работающих в замкнутом цикле с окомкователем. Каждый окомкователь работает в паре с одним грохотом. Грохочение ведётся по классу 9 мм. некондиционные окатыши (циркуляция): мелочь и класс (+ 16 мм), предварительно разрушенный в роторном разрушителе системой конвейеров направляются в окомкователи, а кондиционные на сборные конвейера ОБ –1 и ОБ –2.
1.3 Производство и отгрузка обожженных окатышей
Целью термообработки является упрочнение и максимальное окисление сырых окатышей, обеспечивающее: минимальное образование мелочи при транспортировке окатышей от фабрики до потребителя, учитывая возможность складирование и хранение окатышей на открытых складах, минимальное разупрочнение и разрушение окатышей в условиях восстановительной плавки доменной печи.
Термообработка окатышей осуществляется на обжиговых машинах конвейерного типа ОК – 520 №1 и №2.
Непрерывно движущиеся по рельсам (рабочая и холостая ветви) обжиговые тележки образуют ленту машин. Дно тележек представляет собой колосниковую решётку. Ширина тележек 4 метра. Движение обжиговых тележек на рабочей ветви осуществляется приводными звёздочками, расположенными в головной части машины. Привод машины односторонний, состоит из двух электродвигателей постоянного тока с регулировкой скорости вниз от основной – изменением величины приложенного напряжения, двух цилиндрических четырёхступенчатых редукторов и открытой зубчатой передачи. Машины работают с применением донной и бортовой «постели».
Разгрузочное устройство машины подвесное, с грузовым прижимом к средней части машины. Изменение длины ленты обжиговых тележек под действием температуры компенсируется поворотом разгрузочного устройства вокруг оси подвеса. Все узлы машины смонтированы на сварочном каркасе, состоящим из средней, головной, разгрузочной частей. Для компенсации температурных расширений в средней части каркаса, предусмотрены температурные стыки, разделяющие каркас машины на отдельные блоки. Для предотвращения вредных подсосов атмосферного воздуха в вакуум – камеры и выбивания газов из камер нагнетания предусматривается система бортовых, продольных и поперечных уплотнений между обжиговыми тележками. Тепловая часть машины включает установку горнов с форкамерами, коллектор прямого перетока, газовоздушные камеры разрежения и нагнетания (вакуум – камеры). В головной части машин происходит подача «постели» и сырых окатышей. Бортовая и донная «постели» служат для предохранения от перегрева колосников, бортов и корпусов обжиговых тележек и для защиты колосникового поля от забивания. Во время движения тележек от загрузочной части к разгрузочной сырые окатыши подвергаются: сушке в восходящем потоке (продувом), сушке в нисходящем потоке (прососом), нагреву и обжигу. А так же охлаждению в восходящем и нисходящем потоках. В процессе термообработки сырые окатыши проходят ряд физико-химических процессов: удаление влаги, нагрев, разложение известняка, упрочнение окатышей в результате спекания и рекристаллизации зёрен концентрата, окисления магнетита и образования жидких фаз, охлаждение.
Технологические зоны обжиговой машины.
- В зоне сушке происходит удаление влаги из сырых окатышей и подготовка их к последующему высокотемпературному нагреву. Зона сушки состоит из двух подзон: сушка 1 и сушка 2. Сушка 1 состоит из трёх подзон: сушка 1 (вакуум – камеры №№ 1а, 1, 2) с продувом теплоносителя через слой окатышей, сушка 1а (вакуум - камеры № 3) с прососом теплоносителя, зона сушки 1б (вакуум – камера №4) с прососом теплоносителя.
Температура теплоносителя, подаваемая в зону сушки 1, составляет 220 –320 0С, температура над слоем окатышей 50 – 60 0С.
Хорошо организованная работа зоны сушки обеспечивает высокое качество продукции и производительность обжиговой машины. Критерием работы зоны сушки может служить температура в вакуум – камере №6 (не менее 80 – 90 0С).
В зоне подогрева происходит удаление влаги из нижних горизонтов слоя, разложение карбонатов, окисление магнетита, упрочнение окатышей за счёт твёрдофазного спекания. Зона подогрева расположена над вакуум-камерами №№7 – 9. Для сжигания природного газа в зоне установлено 3 пары горелок. С 1 по 6 горелки погашены и разжигаются при сушке огнеупорной футеровки после ремонта обжиговой машины. Отсос газов осуществляется дымососом Д1.
В зоне обжига происходит завершение в основной массе слоя окатышей процессов окисления магнетита, разложение карбонатов, упрочнение окатышей за счёт образования жидких фаз.
Зона обжига расположена над вакуум-камерами №№10 – 15. В зоне установлено 6 пар горелок и сжигается около 138800нм3/час природного газа в атмосфере первичного (300 0С 11000нм3/час) и вторичного (800 0С 29300 нм3/час) воздуха. Температура над слоем поддерживается на уровне 1240 – 1250 0С средствами автоматики. Разрежение в горне 2 – 5 кгс/м2.
В зоне рекуперации заканчивается процесс обжига в нижних слоях окатышей за счёт переноса аккумулированного верхом слоя тепла к границе «окатыш – постель». Температура нижних горизонтов слоя при этом должна приближаться к значениям температуры над слоем в зоне обжига. Контроль степени прогрева нижних горизонтов слоя осуществляется при температуре отходящих газов, которая должна составлять в вакуум – камерах№№16 –17 400 – 480 0С. В горне зоны рекуперации поддерживается температура 900 –1000 0С и давление 3 – 5 кгс/м2 за счёт перетока горячего воздуха из зоны охлаждения 1 (800 0С, 9200 нм3/ час)
Зона охлаждения разделяется на три подзоны:
Зона охлаждения 1 (в/ камеры №18 – 27 обжиговая машина №1 и в/камеры №№18 – 26 обжиговая машина № 2). Подогретый до 80 0С воздух подаётся из выхлопа дымососа Д3а во всас дымососа Д3. Подогретый воздух продувается через слой снизу, ещё более прогревается и используется в других технологических зонах.
Зона охлаждения 2 (в/камеры 28 –29 обжиговая машина № 1 и в/камеры 27 – 28 обжиговая машина № 2). Атмосферный воздух продувается через слой окатышей снизу, нагревается и используется в других технологических зонах.
Зона охлаждения 2б (в/камеры 28 – 29 обжиговая машина №1). Атмосферный воздух дымососом Д3а просасывается через слой окатышей и с температурой 70 – 80 0С подаётся на всас дымососа Д3а и далее используется в зоне охлаждения 1.
Зона охлаждения 2б (в/камеры №29 – 32 обжиговая машина №2). Атмосферный воздух дымососом Д3а просасывается через слой окатышей и с температурой 70 – 80 0С подаётся в коллектор грязного газа СК – 3 – 1 и далее используется в зоне охлаждения 1.
За счёт реверса воздуха происходит выравнивание температур по высоте слоя окатышей. Температура окатышей на выходе из бункера – выравнивателя не должна превышать 130 0С.
Системы газоочистки на фабрике окомкования
Газоочистные устройства предназначены для очистки до санитарных норм выбрасываемых в атмосферу газов, защиты роторов дымососов от абразивного износа пылью.
Очистка газов, сбрасываемых в атмосферу, осуществляется мокрым способом в установках «труба Вентури» – скруббер – капле отделитель. Перед дымососами Д 4, Д2а установлена сухая газоочистка – циклоны. Батарея циклонов должна быть тщательно герметизирована, а поверхность циклонов закрыта защитным слоем – термоизоляцией.
Технология отгрузки готовой продукции на фабрике окомкования
Обожженные окатыши после обжиговых машин транспортируются системой конвейеров ГР –1,2 (ОК 520 № 1), ГР – 3,4 (ОК – 520 № 2) и распределяются на два потока. Один поток окатышей направляется на реверсивные конвейера ГР – 6,7 и далее подаются либо на конвейера ПБ – 1,2 и в погрузочный бункер объёмом 500 м3 для погрузки в ж.д. вагоны, либо, в случае отсутствия вагонов, на склад. Второй поток направляется конвейерами ГР – 9,10,11,12на грохот «Шенк» для выделения окатышей класса +10 мм так называемой «постели». Надрешёточный продукт класс +10 мм транспортируется конвейерами в бункера донной и бортовой «постели» обжиговых машин. Подрешёточный продукт –10 мм разгружается на конвейера ГР –6,7. При отсутствии вагонов обожженные окатыши направляются на склады (склад №1 – основной ёмкостью около 57 тысяч тонн, склад №1а – резервный ёмкостью около 22,3 тысяч тонн, Склад №2 – ёмкостью 72,4 тысяч тонн, склад №2а – ёмкостью 53,2 тысяч тонн).
Отгрузка окатышей в железнодорожные вагоны осуществляется через бункера – дозаторы погрузочного бункера по двум ж.д. путям № 17 и № 18. На каждый ж.д. путь имеются три бункера объёмом 16,25 м3 каждый.
Отгрузка окатышей со складов 2 и 2а осуществляется укладчиком заборщиком роторным 550/550, конвейерами СО-7, СО-8, СО-3, ГР-8, ПБ-1, ПБ-2, погрузбункер.
2 Расчет шихты для производства окатышей
Для расчета шихты необходимо знать:
· Содержание FeO в обожженных окатышах 0,9% исследуем. до 3%
· Степень выгорания серы: 50%
· Основность обожженных окатышей 0,2
· Расход бентонита 0,4кг (на 100кг окатышей) или келловейской глины 0,5 100кг окатышей
· Химический состав используемых минералов.
Порядок расчета
Принимаем химический состав компонентов шихты согласно просчитанным данным и приводим в виде таблицы (приложения, таблица 2.1)
Проверка суммы компонентов химического состава сырых материалов на 100%
В химических составах минералов указывается содержание исходных элементов в свободном состоянии. Поэтому если сложить число отражающим содержание всех компонентов химического состава того или другого материала, то сумма их будет <100%.
Сводимость же материального баланса возможна лишь при равенстве всех составляющих химического состава 100%.
Химический состав компонентов шихты приведены в приложениях Таблица 2.1
Полный химический состав шихтовых минералов приведены в приложениях Таблица 2.2
Расчёт полного химического состава шихтовых материалов производим по формуле:
где Эм – содержание свободного элемента в материале, %;
См – содержание элемента по данным х/а, %;
Э – молекулярная масса элемента в соединении;
М – молекулярная масса соединения.
Пересчет состава концентрата 
В закись железа FeO связного железа:
Количество железа, находящегося в окиси железа Fe2O3 определяется по разности между общим его содержанием в концентрате и связующим с FeO Feоб – FeO =63,6-16,528=47,072
В концентрате содержится окиси железа:
или Feоб=Fe2O3+FeO
содержание окиси фосфора:
содержание окиси марганца:
. Определяем сходимость на 100%
Пересчитываем химический состав концентрата на 100%
% P2O5 %

Пересчитываем химический состав известняка на 100%
В закиси FeO содержится железа:
Fe2O3=Feоб – FeO =0.39-0.08=0.31%
В известняке содержится
Содержание фосфора:
Содержание оксида марганца:
..1.1
..1.2 Определяем сходимость на 100%
Пересчитываем химический состав известняка на 100%
Пересчитываем состав келловейской глины
Содержание Р2О5:
Содержание Мn:
Определяем сходимость на 100%
Пересчитываем химический состав келловейской глины на 100%
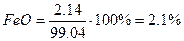
1 Определение расхода концентрата и известняка на производство 100 кг обоженных окатышей сводится к совместному решению:
1.Уравнение материального баланса.
2.Баланса основности.
3.
Составляем систему 2-х уравнений с 2 неизвестными:
обозначаем: х – расход концентрата, кг
у – расход известняка, кг
б – расход глины, кг
2.1Составляем 1-е уравнение
..1.2.1.1.1.1 а – количество шихты для получения 100,0 кг окатышей
х – расход концентрата, на 100,0 кг окатышей
у – расход известняка, кг на 100,0 кг окатышей
ах, ау, ав – потери массы концентрата, известняка, бентонита см. таблица 3
Потери массы компонентов в шихте при обжиге приведены в приложениях Таблица 2.3
В действительности окатышей будет меньше, т.к. неучтены потери кислорода ао2, теряемого шихтой при восстановлении и термической диссоциации, те чтобы получить 100,0 кг окатышей нужно взять не А, а А – а О2, кг шихты. А – ао2=100 или А – 100=ао2
Для составления материального баланса необходимо вычислить потери кислорода при обжиге. Из исходных данных принимаем содержание закиси железа в готовых окатышах: (1,0% FeO), по реакции 2Fe2O3 → 4FeO+O2, имеем соотношение: [4·(56+16)-2·16]=[288-32], т.е. при образовании 288кг FeО в окатышах можно определить и количество выделившегося кислорода, оно в девять раз:(288:32-9) меньше массы закиси железа, тогда потери на ао2 при обжиге составят:
где FeOоо – содержание FeO в обожженных окатышах
Feox, Feоу, Feог – содержание FeO в концентрате, известняке, глине.
Тогда уравнение материального баланса будет:
0,993х+0,574у+0,886г-100=0,11-0,023х-0,0001у-0,002г
1,016х+0,5741у+0,888г=100,11
1,016х+0,5741у+0,888·0,5=100,11
1,019х+0,5741у+0,444=100,11
1,019х+0,5741у=99,67 (1-е уравнение вида ах+ву=с)
а в с
Другое уравнение составляем по основности окатышей, которое должно быть равно:
2-е уравнение имеет вид:
0,46х+58,68у+8,51г=0,21(10,18х+2,35у+67,89)
0,46х+58,68у+4,255=2,138х+0,493у+7,12
-1,678х+58,187у= 2.865
(2-е уравнение вида а1х+в1у=с1)
Получим систему уравнений:
Решаем систему уравнений с двумя неизвестными, через определители:
Определяем неизвестные:
(расход концентрата)
(расход известняка)
Проводим проверку основности шихты по данным расчета:
3.Определяем % соотношение составляющих сухой шихты по уравнениям:
концентрат – 96,3% - 96,3%
известняк - 2,82% - 2,82%
глина - 0,49% - 0,49%
всего 99,61% 99,61%
Рассчитываем количество компонентов, вносимой сухой шихтой в окатыши:
с концентратом выходит:
с известняком выходит:
с глиной выходит:
Определяем состав обоженных окатышей
Для определения химического состава обоженных окатышей составляется таблица 4.
при составлении таблицы оперируем данными расчета массы концентрата, известняка, глины, потребными для получения 100 кг окатышей которые заносятся в графу, расход сухого материала.
при составлении балансовой таблицы необходимо помнить, что графа содержится в сырых окатышах находится суммированием масс отдельных компонентов в концентрате, известняке, глине:
∑Fe=КкFe+КиFe+КгFe=61.37+0.011+0.021=61.4 кг
Например:
∑FeO=KkFeO+KkFeO+KгFeO=19.94+0.0022 +0.011= 19.9кг
∑Fe2O3=KkFe2O3+KиFe2O3+KгFe2O3=65+0.024+0.023= 65.047кг
4.3 Графа «переходит в обоженные окатыши» заполняется по данным графы. Содержание в сырых окатышах при этом учитывается, в процессе обжига окатышей из них удаляется 50-75% серы. Повышение температуры и времени обжига, уменьшение основности окатышей способствует лучшей десульфации окатышей, так как с одной стороны уменьшаетcя возможность образования СаSO4, с другой стороны увеличивается упругость её диссоциации.
Количество компонентов вносимых обоженные окатыши и переходящие в нихпоказан в приложении Таблица 2.4
Принимаем, что в обоженные окатыши переходит 62% серы, от ее содержания в сырых окатышах. В окатыши переходит серы:
Условно, полагаем, что вся сера в офлюсованных окатышах связана в серный ангидрид SO3 и находится в окатышах в виде CaSO4.
В окатышах содержится:
Количество FeO и Fe2O3 в обоженных окатышах не остается таким, каким оно было в сырых окатышах, а изменяется в соответствии с режимом обжига: увеличение температуры обжига и времени пребывания окатышей в зоне обжига приводит к повышению содержания FeO т.е. степени окисленности окатышей и уменьшения содержания в них серы.
Принимаем содержание FeO=1,0% степень окисленности этих окатышей характеризуется отношением Feоб: Fe++ и составляет от
5-20
Принимаем степень окисленности равной 5.
В обоженных окатышах будет:
двухвалентного желез
трехвалентного железа:
В окатышах содержится:
оксида железа FeO
оксида железа Fe2O3
4.5 Графа «Состав обоженных окатышей» определяется по формуле:
Проводим проверку на сходимость суммы компонентов на 100%
∑=16,2+70.63+10,14+2,22+0,264+0,15+0,0045+0,02+0,041+0,205+0,0766=99.95%
Определяем массу сухой и увлажненной шихты
Масса влажного материала при известном расходе сухого определяется по формуле:
где: Qвл, Qс – масса влажного и сухого материала шихты, кг
W – влажность материала, %
Оптимальная влажность сырых окатышей из магнетитовых концентратов, обеспечивает хорошую прочность окатышей, находится в пределах 8,8-9,2% Принимаем влажность окатышей равной 11%
Составы сухой и увлажненной шихты приведены в приложениях Таблица 2.5
Количество влаги определяется по формуле:
Масса увлажненной шихты определяется по уравнению:
В шихте содержится гигроскопической влаги (вода на увлажнение):
111,13-98,91=12,22кг
Составление баланса по железу и кислороду окислов железа в окатышах
Процесс обжига окатышей по отношению к железу может быть:
- восстановительным;
- окислительным.
в результате окислительного процесса количество кислорода, связанного в окислы железа повышается, а восстановительного – понижается.
С целью определения направленности процесса обжига составляем баланс по железу и кислороду оксидов железа, который представлен в таблице 6.
Баланс составляется на основании данных таблицы 4. с использованием для пересчетов соответствующих уравнений.
При составлении таблицы 6. необходимо иметь в виду, что количество железа в сырых и обоженных окатышах должно быть одинаково, так как в процессе обжига железо постоянно переходит в обоженные окатыши и соответствовать таблице 4. Неувязка баланса допускается не >±0,1 кг.
Баланс по железу и кислороду оксидов железа в окатышах, кг
приведены в приложениях Таблица 2.6
Определяем Fe в оксиде железа:
Определяем массу О2 в оксиде железа:
Определяем массу Fe в оксиде железа:
Определяем массу О2 в оксиде железа:
Определяем массу Fe и О2 в сырых и обоженных окатышах.
Масса О2 кислорода в оксидах железа повысилась.
24,14 – 23,934 =0,206кг
Значит, процесс по отношению к железу является окислительным и при обжиге окатышей будет выделять дополнительное тепло.
Участвует железо в образовании Fe2O3:
48,16 – 45,533=2.63кг
из них по реакции:
4FeO+O2=2Fe2O3
15,48 – 12,3=3,18кг
по реакции:
4Fe+3O2=2Fe2O3
3,18 – 2.63=0.55кг
3 Специальная часть
3.1 Влияние связующих добавок на пористость обожженных окатышей и на их металлургические свойства
Влияние флюсующих добавок.
Российская федерация является первой страной в мире по разработке и по освоению технологии производства офлюсование окатышей.
Степень офлюсование характеризуется основностью, которая определяется отношением CaO/SiO под термином – офлюсованные окатыши, полученные из смеси концентратов и флюсующей добавки для достижения оптимального соотношения CaO/SiO .
Для окатыша эта величина колеблется в пределах от 0.15 до 1.27. основным назначением флюсов является обеспечение ошлакования всей пустой породы содержащейся в руде, золе кокса, и других компонентов доменной шихты. Целесообразность производства офлюсованных окатышей определяется в первую очередь необходимостью более эффективного использования полезного объёма доменной печи, благодаря исключительно сырого известняка из состава шихты.
Офлюсование агломерата не может полностью решить вопрос вывода сырого известняка из шихты, вследствие снижения производительности агломерационных машин ухудшения удаления серы при изготовлении офлюсованного агломерата.
В последние годы развитие теории и практики производства окатышей позволило начать повсеместное внедрение офлюсования на ФОКе.
В качестве флюсующих добавок обычно применяют известняк, доломит, реже гашеную и не гашеную известь. Обычно окатыши могут иметь основность 0.15 – 1.27. принятое содержание в известняке 53 % CaO и 4.5 % CO . Количество известняка в шихте зависит от основности в шихте и содержании кремнезёма в концентрате можно определить по монограмме.
На ФОКах России флюсы поступают не подготовленными, в виде плотных кристаллических разновидностей 5(10) – 50(80) мм. После дробления в конусной или молотковой дробилке и измельчения в вентилируемых шаровых мельницах с подсушкой известняк представляет собой легко сыпучий порошок.
На окомковательной фабрике, вследствие естественной офлюсованности концентрата, и низкого содержания в нем кремнезёма (для получения окатышей основностью 1.2 %) достаточно в шихту добавить 7% известняка.
Это позволяет измельчать известняк до содержания 75 – 80 % класса <0.074 мм (2500 – 3000 см /г)
При получении окатышей основностью 1 – 1.5 из кремнистых концентратов содержащих >8 % SiO добавка известняка должна составлять 15 – 17 % от массы сухого концентрата. В этом случае необходимо измельчать содержание 90 – 95 % класса <0.05 мм. (4500 – 5200 см /г)
Влияние флюсующих добавок на пористость и металлургические свойства обожженных окатышей можно представить в виде графиков.
Содержание известняка в шихте должно составлять 22 – 24 %, так как уменьшение содержания известняка ведет к уменьшению пористости и к снижению качества обоженых окатышей.
А содержание известняка в шихте более 24 % ведет к увеличению пористости, что так же пагубно сказывается на качество обожженных окатышей.
Влияние упрочняющих добавок.
В качестве упрочняющих добавок на ФОКе применяют глину. Свойство глинистой породы определяется ее составом и относительным содержанием всех входящих в нее минералов. Для промышленного использования имеют значение следующие свойства глин: гидрофильность, способность к гидрофильность и диспергированию, влагоемкость, набухаемость, ионообменная способность, способность давать устойчивые суспензии.
Гидрофильность. Характеризуется способностью веществ сортировать на своей поверхности воды. Сорбционная способность глинистых минералов зависит от субмикроскопической структуры слагающих его частиц.
Способность к диспергированию при смачивании водой.
Бентонитовые глины являются мелкопористыми материалами. Общая пористость отдельных образцов различных разновидностей бентонитовых глин достигает 25 %. Анализ структуры пор показал, что с большими удельными поверхностями преобладают переходные поры и микропоры. При смачивании бентонитов водой ее молекулы проникают по капиллярам к первичным частицам, а затем в межслоевые промежутки. Благодаря давлению водные прослойки утолщаются, происходит удаление частиц друг от друга вплоть до полного их разобщения. Глина как бы самопроизвольно измельчается, диспергирует.
Диспергирование глин способствует перемешиванию и всякого рода механические воздействие. На эту способность оказывает влияние и катионы щелочных и щелочноземельных металлов, поскольку они определяют толщину пленки адсорбированной воды. Например, небольшие количества натрия в глине способствуют образованию толстых пленок связанной воды, постепенно сменяющих свободной.
Водные суспензии щелочных бентонитов обладают способностью обратимо разжиматься при механических воздействиях.
Влагоемкость.
Характеризует способность глины впитывать влагу. Эта способность у бентонитовых глин сильно развита. Наиболее влагоемкими являются истинные щелочные бентониты, так как они содержат примерно в 5 раз больше связанной воды, чем щелочноземельные. Капиллярная и максимальная молекулярная влагоемкость у бентонита составляет соответственно 85 – 92 и 40 – 45 %.
Высокая влагоемкость бентонитов связана, прежде всего, с внутренней кристаллической адсорбцией и возможностью изменения кристаллической структуры глинистых минералов в процессе самой адсорбции. Щелочноземельные бентониты обладают значительно меньшей влагоемкость, чем щелочные.
Водоадсорбирующие свойства бентонитов сильно ухудшаются в случае покрытия поверхности отдельных ячеек органическими ионами.
Последние, в дополнение к кулоновским силам, удерживаются на поверхности ячеек силами. Чем больше органический ион, тем сильнее уменьшается водоадсорбирующая емкость бентонита.
Набухаемость.
Характеризуется способностью бентонитовых глин поглощать воду и значительно увеличиваться в объеме. Природа набухания изучена недостаточно, и нет еще теории, объясняющей это явление. Принято, что в основе набухания лежит действие адсорбированных, осмотических и капиллярных сил. Изучение кинетики набухания показывает, что у большинства глин набухание практически заканчивается за 24 часа. Набухание особенно интенсивно проходит в первые 2 – 3 часа. Набухание особенно уплотненных глинистых материалов проходит очень быстро и длится, вероятно, минуты.
Наибольшей набухаемостью в водной среде обладают истинные щелочные бентониты. Эти бентониты способны впитывать более чем десятикратные количества воды, увеличиваясь при этом в объеме свыше 15 – 20 раз по сравнению с первоначальным. Большое отрицательное влияние на набухаемость этих бентонитов оказывает наличие в них растворимых в воде солей, особенно щелочноземельных металлов.
Ионообменная способность.
В бентонитовых глинах имеются катионы щелочных и щелочноземельных металлов. От их количества и состава зависят свойства глин. Бентонитовые глины имеют различную ионообменную способность как по величине емкости обмена, то есть сумме всех обменных катионов (и по содержанию каждого катиона отдельно), так и по местам расположения ионов, способных к замещению.
Не нашли, что искали? Воспользуйтесь поиском:
|