Главная
Популярная публикация
Научная публикация
Случайная публикация
Обратная связь
ТОР 5 статей:
Методические подходы к анализу финансового состояния предприятия
Проблема периодизации русской литературы ХХ века. Краткая характеристика второй половины ХХ века
Ценовые и неценовые факторы
Характеристика шлифовальных кругов и ее маркировка
Служебные части речи. Предлог. Союз. Частицы
КАТЕГОРИИ:
|
Требования к ограничению распространения пожара на производственном объекте 2 страница
№ опыта
| Содержание Fe общ., %
| Доля аглоруды в ж.р.с., %
| Массовая доля компонента, %
| Основность*
| концентрат
| аглоруда
| Fe
| FeO
| CaO
| SiO2
| S
|
| 65,0
| 54,0
|
| 62,9
| 0,49
| 0,61
| 8,77
| 0,0018
| 0,096
|
|
| 62,6
| 0,47
| 0,68
| 9,17
| 0,0020
| 0,098
|
|
| 62,5
| 0,61
| 0,69
| 9,24
| 0,0020
| 0,098
|
|
| 62,3
| 0,62
| 0,73
| 9,41
| 0,0031
| 0,100
|
| 65,8
| 54,0
|
| 63,6
| 0,54
| 0,65
| 7,97
| 0,0018
| 0,107
|
|
| 63,1
| 0,55
| 0,72
| 8,44
| 0,0027
| 0,105
|
|
| 63,0
| 0,50
| 0,75
| 8,58
| 0,0030
| 0,105
|
|
| 62,8
| 0,50
| 0,75
| 8,78
| 0,0036
| 0,104
|
| 65,4
| 52,6
|
| 63,5
| 0,68
| 0,63
| 8,15
| 0,0018
| 0,093
|
|
| 63,2
| 0,56
| 0,66
| 8,81
| 0,0024
| 0,093
|
|
| 62,8
| 0,66
| 0,70
| 8,70
| 0,0025
| 0,093
|
|
| 62,3
| 0,36
| 0,70
| 9,10
| 0,0038
| 0,093
|
| 65,8
| 52,6
|
| 63,4
| 0,40
| 0,52
| 7,86
| 0,0016
| 0,097
|
|
| 63,1
| 0,42
| 0,55
| 8,42
| 0,0019
| 0,096
|
|
| 63,2
| 0,39
| 0,55
| 8,44
| 0,0022
| 0,096
|
|
| 62,8
| 0,43
| 0,60
| 9,02
| 0,0032
| 0,096
| * - основность окатышей, рассчитанная по формуле (СаО+MgO)/SiO2
Таблица 3.6 – Результаты расчета шихты при использовании богатой руды в шихте для производства окатышей
| Доля богатой руды (с качеством 54% Fe) в концентрате, %
| Показатели
|
|
|
|
|
|
|
|
|
|
|
|
| Кач-во концентрата:
|
|
|
|
|
|
|
|
|
|
|
|
| мас. доля, %: железо
| 65,1
| 65,4
| 65,8
| SiO2
| 8,65
| 8,35
| 8,00
| Качество окатышей, %:
|
|
|
|
|
|
|
|
|
|
|
|
| железо
| 63,01
| 62,66
| 62,52
| 62,31
| 63,30
| 62,95
| 62,90
| 62,70
| 63,7
| 63,36
| 63,23
| 63,05
| SiO2
| 8,77
| 9,14
| 9,29
| 9,51
| 8,48
| 8,86
| 9,01
| 9,25
| 8,15
| 8,51
| 8,65
| 8,85
| сера
| 0,002
| 0,006
| 0,008
| 0,010
| 0,002
| 0,006
| 0,008
| 0,010
| 0,002
| 0,006
| 0,008
| 0,010
| Основность
| 0,091
| 0,092
| 0,093
| 0,094
| 0,094
| 0,095
| 0,096
| 0,097
| 0,107
| 0,105
| 0,105
| 0,104
|
| база
|
|
|
|
|
|
|
|
|
|
|
| Производительность (расч.), т/ч
|
| 616,2
| 615,4
| 614,3
| 618,0
| 616,2
| 615,4
| 614,3
| 618,0
| 616,2
| 615,4
| 614,3
| Дополнит.к базе расход газа на обжиг, м3/т ок.
|
| 0,462
| 0,651
| 0,934
|
|
|
|
|
|
|
|
|
|
|
|
|
|
|
|
|
|
|
|
|
|
| Доля богатой руды (с качеством 52,6% Fe) в концентрате, %
| Показатели
|
|
|
|
|
|
|
|
|
|
|
|
| Кач-во концентрата:
|
|
|
|
|
|
|
|
|
|
|
|
| - мас. доля, % - железо
| 65,4
| 65,7
| 66,00
| SiO2
| 8,38
| 8,08
| 7,78
|
|
|
|
|
|
|
|
|
|
|
|
|
| Качество окатышей, %:
|
|
|
|
|
|
|
|
|
|
|
|
| железо
| 63,34
| 62,86
| 62,69
| 62,42
| 63,59
| 63,14
| 62,96
| 62,68
| 63,88
| 63,41
| 63,23
| 62,95
| SiO2
| 8,51
| 9,03
| 9,23
| 9,55
| 8,22
| 8,75
| 8,96
| 9,28
| 7,92
| 8,47
| 8,69
| 9,02
| сера
| 0,002
| 0,006
| 0,008
| 0,010
| 0,002
| 0,006
| 0,008
| 0,010
| 0,002
| 0,006
| 0,008
| 0,010
| Основность
| 0,093
| 0,093
| 0,093
| 0,093
| 0,097
| 0,096
| 0,096
| 0,096
| 0,100
| 0,099
| 0,099
| 0,099
|
|
|
|
|
|
|
|
|
|
|
|
|
| Производительность (расч.), т/ч
| 618,0
| 616,2
| 615,4
| 614,3
| 618,0
| 616,2
| 615,4
| 614,3
| 618,0
| 616,2
| 615,4
| 614,3
| Дополнит. к базе расход газа на обжиг, м3/т ок.
|
| 0,465
| 0,651
| 0,932
|
|
|
|
|
|
|
|
| | | 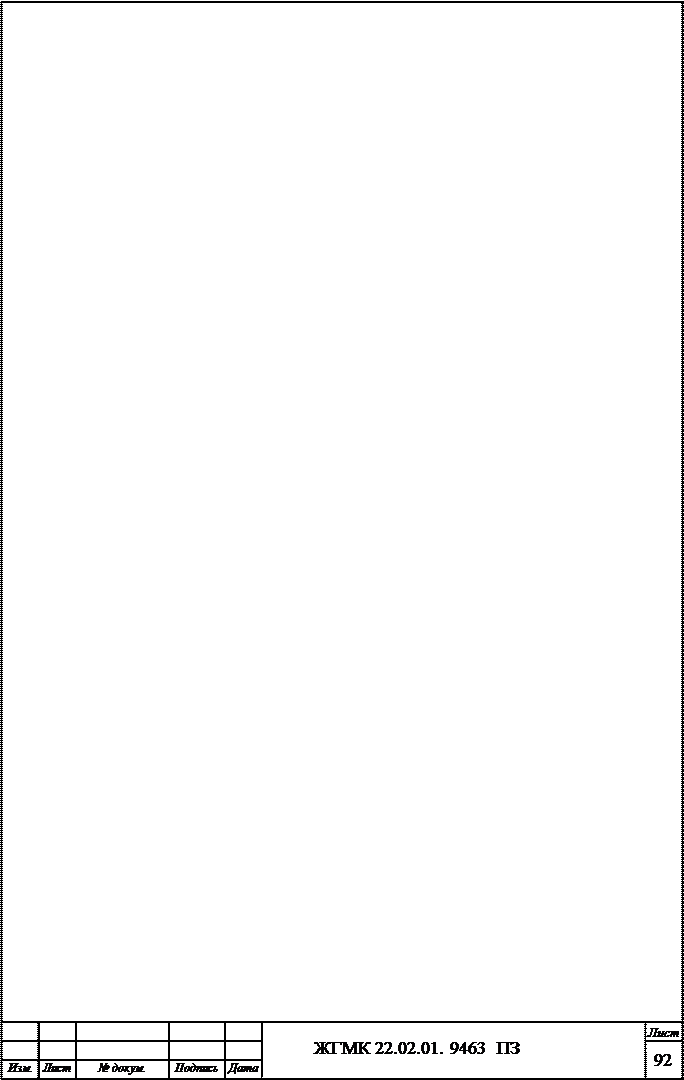 |
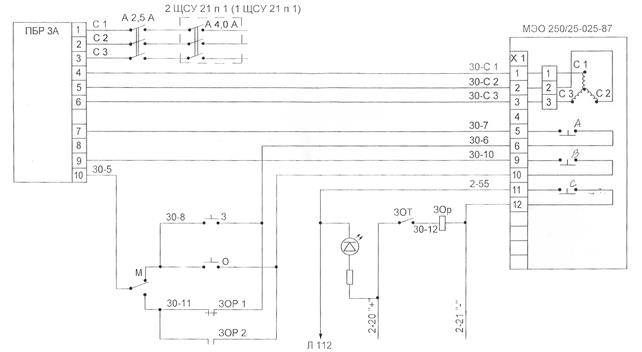
Рисунок 3.1 Принципиальная электрическая схема управления дросселями на вентиляционных газоходах из бункеров известняка и бентонита
Приложение 4
Таблица 4.1 - Технологические требования к концентрату
Параметры
| Величина
| Массовая доля Fe, %
| по месячной программе
| Массовая доля класса -0,074 мм, %
| по месячной программе
| Массовая доля влаги, %
| 10,2 (10,1)
| Минимальное значение массовой доли Fe за смену, %
|
| Минимальное значение влаги (массовой доли H2O) за смену, %
|
| Максимальное значение H2O, %
| 10,35
| Удельная поверхность концентрата, см2
| не менее 1800
| Массовая доля SiO2 за месяц, %
| 8,5
| Таблица 4.2 - Технологические требования к известняку
Параметры
| Величина
| Массовая доля CaO, %
|
| Массовая доля класса -0,074 мм, %
|
| Массовая доля H2O, %
|
| Допустимое отклонение по:
|
| Классу -0,074
|
| Влаге
|
|
Таблица 4.3 - Технологические требования к бентонитовой глине
Параметры
| Величина
| Массовая доля CaO, %
|
| Массовая доля SiO2, %
|
| Массовая доля класса -0,074 мм, %
|
| Массовая доля влаги, %
|
| Набухаемость, у.е.
|
| Допустимое отклонение:
|
| по классу -0,074
|
| по влаге
|
|
Таблица 4.4 - Технологические требования к сырым окатышам
Наименование показателей
| Норма
| Массовая доля влаги, %
| 9,6÷9,8
| Прочность на раздавливание, кг/ок
| не менее 1,3
| Число сбрасываний на металлургическую плиту с высоты 500 мм, раз
|
не менее 3,5
|
Таблица 4.5 - Внутренние технические требования
№п/п
| Наименование показателей
| Норма
|
|
ИЗВЕСТНЯК МОЛОТЫЙ
Массовая доля CaO, %
Массовая доля класса минус 74 мкм, %
Массовая доля влаги, %
БЕНТОНИТ
Массовая доля класса минус 74 мкм, %
Массовая доля влаги, %
Набухаемость, мл/г
Вязкость 10% суспензии, мПа·с
Индекс набухания, мл/2г
СЫРЫЕ ОКАТЫШИ
Массовая доля влаги, %
Прочность на раздавливание за смену, кг/ок
Допустимое отклонение по массовой доле влаги по экспресс-анализам, %
Допустимое отклонение по прочности на раздавливание в экспресс-анализах, кг/ок
Число сбрасываний на металлическую плиту с высоты 500 мм за смену, раз
Допустимое отклонение прочности на сбрасывание в экспресс-анализах, раз
|
не менее 52,0
не менее 89,0
не более 0,4
не менее 88,0
не менее 6,0
не менее 14,0
не менее 30,0
не менее 28,0
9,6÷9,75
1,3
-0,05;+0,05
-0,05
3,5
-0,2
| Таблица 4.6 - Технологические требования к качеству обожжённых
окатышей
Наименование показателей
| Норма
| Методы испытаний
| 1 Массовая доля железа за месяц, средняя, %
| по программе месяца
| ГОСТ 23581.18
| 2 Допустимое отклонение по массовой доле железа за смену от среднего, %
|
- 0,2
|
| 3 Основность за месяц, средняя, ед.
| по программе месяца
| (факультативно)
| 4 Допустимое отклонение по основности за смену от среднего, ед.
| + 0,025
|
| 5 Массовая доля класса 5-16 мм за месяц, %, не менее
| 90,0
| ГОСТ 27562
| 6 Массовая доля класса 0-5 мм за месяц, средняя, %
| по программе месяца
| ГОСТ 27562
| 7 Массовая доля SiO2 за месяц, средняя, %, не более
| по программе месяца
| ГОСТ 23581.16
(факультативно)
| 8 Показатель прочности за месяц, средний:
|
|
| - на удар (выход класса +5 мм), %
| 92,0
| ГОСТ 15137
| - на сжатие, кг/окатыш
| 225,0
| ГОСТ 24765
| 9 Допустимые отклонения в экспресс-анализах от среднего за месяц по показателю прочности на удар
|
- 4,0
|
| 10 Показатель истираемости (выход класса – 0,5мм) за смену, %, не более
|
6,0
| ГОСТ 15137
|
Таблица 4.7 - Химический и гранулометрический состав окатышей
Наименование показателей
| Норма
| Методы испытаний
| 1 Массовая доля железа общего, %
| 66,0
| ГОСТ 23581.18
| 2 Допустимое отклонение по массовой доле железа, %
| -1,0
|
| 3 Массовая доля класса 5-16 мм, %, не менее
| 85,0
| ГОСТ 27562
| 4 Массовая доля класса 0-5 мм, %, не более
| 5,0
| ГОСТ 27562
| 5 Прочность на сжатие, кг/окатыш, не менее
| 220,0
| ГОСТ 24765
| 6 Показатель прочности, %, не менее
| 9,0
| ГОСТ 15137
| 7 Показатель истираемости, %, не более
| 86,0
| ГОСТ 15137
| Таблица 4.8 - Режимная технологическая карта производства окатышей на фабрике окомкования
Наименование показателей
| Ед.изм.
| Флотоокатыши
| Рядовые окатыши
| Участок шихтоподготовки:
|
|
|
|
|
| Шаровая загрузка мельниц
| т
|
| в т.ч. с диаметром загружаемых шаров 40 мм
| т
| 60 мм
| т
| Материал
|
| Известняк
40.. 60
850..950
200..400
| Бентонит
20..30
500..700
400..600
| Производительность по сырому материалу
| т/ч
| Температура в топке
| º С
| Температура в смесительной камере
| º С
| Температура сушильного агента за мельницей
| º С
|
40..80
50±30
100..500
| Разрежение в топке
| кгс/м2
| Перепад давления на мельнице
| кгс/м2
| Конечная влажность материала
| %
| не более 0,4
| не менее 6,0
| Массовая доля класса минус 74 мкм, не менее
| %
|
89,0
|
88,0
| Индекс набухания, не менее
| мл/2г
|
|
| 26,0
| Эффективная вязкость 10%-й суспензии, не менее
|
мПа*с
|
|
|
30,0
| Участок сырых окатышей
|
|
|
|
|
| Производительность барабана по сырым окатышам
| т/ч
|
|
| 100÷125
| Количество циркуляционной нагрузки по отношению к массе сырых окатышей
| %
|
|
| 150÷250
| Число оборотов барабана
| об/мин.
|
|
| 6 ÷ 10
| Число оборотов роликов грохота
| об/мин.
|
|
| 1000÷1200
| Ширина щели между роликами просеивающей поверхности, не более
| мм
|
|
| 11,0
| Расход бентонита в шихту
| %
|
|
| 0,5 ÷ 0,7
| Расход известняка в шихту
| %
|
|
| по расчету
| Качество сырых окатышей:
|
|
|
|
| - массовая доля влаги
| %
|
|
| 9,6 ÷ 9,8
| - прочность на раздавливание, не менее
| кг/ок
|
|
| 1,3
| - количество сбрасываний с высоты 500 мм на металлическую плиту, не менее
| раз
|
|
| 3,5
| - массовая доля класса 0-5 мм, не более
| %
|
|
| 1,5
| - массовая доля класса 5-16 мм, не менее
| %
|
|
| 85,0
| Доля отсева сырых окатышей из-под роликового укладчика в шихте, не более
|
|
|
| 20,0
| Участок обжига
|
|
|
|
| Высота слоя окатышей
| мм
|
|
| 375 ÷ 410
| Производительность по обожженным окатышам
| т/ч
|
|
| 500 ÷ 600
| № обжиговой машины
|
|
|
|
|
| Температура в колпаке зоны сушки I
| º С
|
|
| 45.. 70
| Разрежение в зоне сушки I
| кгс/м2
|
|
| -30.. -70
| Температура в вакуум-камерах № 1-2
| º С
|
|
| 200.. 300
| Давление в вакуум-камерах №1÷2
| кгс/м2
|
|
| 450.. 650
| Температура в горне зоны сушки IA
| º С
|
|
| 200.. 350
| Температура в горне зоны сушки II
| º С
|
|
| 500.. 650
| Температура в горне зоны подогрева
| º С
|
|
| 700.. 1100
| Температура в горне зоны обжига
| º С
|
|
| 1100..1300
| Давление в горне зоны сушки IA
| кгс/м2
|
|
| -5.. -20
| Давление в горне зоны сушки II
| кгс/м2
|
|
| -2.. -16
| Давление в горне зоны подогрева
| кгс/м2
|
|
| -5.. -16
| Давление в горне зоны обжига
| кгс/м2
|
|
| -0,3..-13
| Температура в вакуум-камерах № 3÷7
| º С
|
|
| 90.. 200
| Температура в вакуум-камерах № 8÷12
| º С
|
|
| 100.. 320
| Температура в вакуум-камерах № 13÷18
| º С
|
|
| 350.. 520
| Разрежение в вакуум-камерах № 3÷7
| кгс/м2
|
|
| -300.. -500
| Разрежение в вакуум-камерах № 8÷12
| кгс/м2
|
|
| -350..- 600
| Разрежение в вакуум-камерах № 13÷18
| кгс/м2
|
|
| -150.. -400
| Температура в горне зоны рекуперации
| º С
|
|
| 1100.. 950
| Температура в горне зоны охлаждения I
| º С
|
|
| 1100.. 700
| Температура в горне зоны охлаждения II A
| º С
|
|
| 700.. 400
| Температура в горне зоны охлаж. II Б
| º С
|
|
| 300..200
| t окр.возд.
| Давление в горне зоны рекуперации
| кгс/м2
|
|
| 2.. 8
| Давление в горне зоны охлаждения I
| кгс/м2
|
|
| 5.. 12
| Давление в горне зоны охлаждения II A
| кгс/м2
|
|
| -5.. -50
| -5.. -120
| Давление в горне зоны охлаждения II Б
| кгс/м2
|
|
| 0.. -10
| -10.. -1200
| Температура в вакуум-камерах № 19-23
| º С
|
|
| 150.. 200
| 20.. 100
| Температура в вакуум-камерах № 24-28
| º С
|
|
| 20.. 100
| t окр. возд.
| Температура в вакуум-камерах № 29-32
| º С
|
|
| t окр. возд.
| 80.. 120
| Давление в вакуум-камерах № 19 – 23
| кгс/м2
|
|
| 300.. 450
| 250 - 450
| Давление в вакуум-камерах № 24 – 28
| кгс/м2
|
|
| 200.. 350
| 250.. 450
| Давление в вакуум-камерах № 29 – 32
| кгс/м2
|
|
| 250.. 450
| -300.. -400
| Температура на конвейерах ГР 1 - 4
| º С
|
|
| 70 – 130
| Температура перед дымососами:
|
|
|
|
| Д1
| º С
|
|
| 60.. 70
| Д1А
| º С
|
|
| 60.. 80
| Д2А
| º С
|
|
| 240.. 320
| Д3
| º С
|
|
| 20.. 80
| Д3’
| º С
|
|
| t окр. Воздуха
| Д3А
| º С
|
|
| 150.. 200
| Д4
| º С
|
|
| 250.. 350
| Д5
| º С
|
|
| 45.. 80
| Д6
| º С
|
|
| 25.. 80
| | | | | | | | | | | | 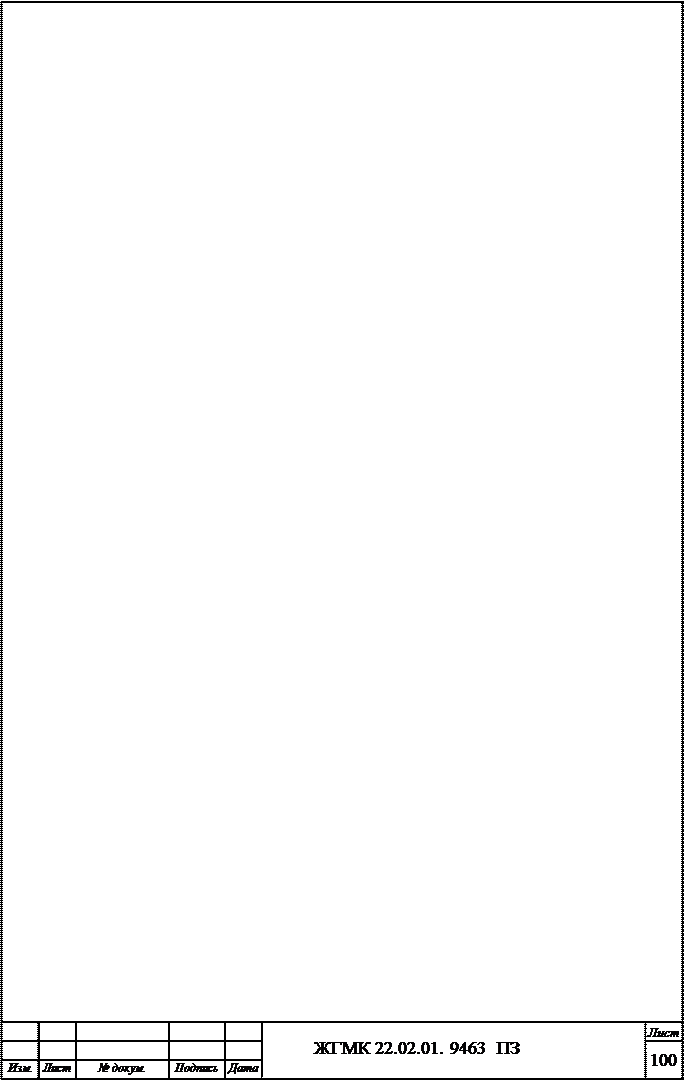 | Приложение 5
Не нашли, что искали? Воспользуйтесь поиском:
|