V. Расчет режимов резания. а — выбрать или рассчитать глубину резания для каждого перехода и прохода;
а — выбрать или рассчитать глубину резания для каждого перехода и прохода;
б — определить расчетом или выбрать значение подачи;
в — выбрать материал режущей части резцов и их период стойкости. Для каждого из выбранных резцов указать углы в плане;
г — рассчитать скорость резания, допускаемую режущим инструментом при выбранном периоде стойкости; определить рас-четную частоту вращения шпинделя станка в минуту по полученной расчетом скорости резания; выбрать ближайшую минимальную к расчетной частоту вращения шпинделя из паспорта станка и по ней определить фактическую скорость резания;
д — рассчитать силу резания для прохода с максимальной глубиной резания и максимальной подачей;
е — сравнить расчетную силу резания (осевую силу) с допускаемой прочностью механизма подачи станка;
ж — определить мощность, необходимую для осуществления процесса резания, и сравнить ее с мощностью электродвигателя станка;
з — определить основное технологическое время на обработку каждого перехода.
VI. Обработка на токарных станках
Расчет режимов резания выполняют по каждому переходу. Если переход состоит из двух проходов — чернового (предварительного) и чистового (окончательного), то скорость резания и число оборотов шпинделя станка рассчитывается для каждого прохода отдельно. Если число черновых проходов более двух, то скорость резания и число оборотов шпинделя станка для второго и последующих черновых проходов не рассчитывают. В этих случаях задаются числом оборотов шпинделя первого чернового прохода и рассчитывают по нему фактическую скорость резания.
В качестве первого перехода при точении всегда выполняется подрезка торца. Если выбранная заготовка закрепляется только в патроне станка, то подрезка торца проводится при закреплении на установочную длину. При закреплении заготовки в патроне и заднем центре станка, подрезка торца проводится при установке заготовки с вылетом от патрона на 5—10 мм.
При закреплении заготовки в заднем центре на ее торцевой поверхности необходимо выполнить центровочное отверстие для закрепления заднего центра. Поэтому, после подрезки торца следующий переход — центрование отверст ия специальным центровочным сверлом. При выполнении данного перехода задаются числом оборотов шпинделя станка при подрезке торца, а скорость резания, глубину резания и технологическое время не рас- 14 считывают. Подачу выполняют вручную и поэтому технологическим временем задаются в пределах 5-10 секунд.
Глубина резания — это толщина слоя металла, срезаемого за один проход резца. Обозначается t, мм. Выбор глубины резания зависит от требуемого класса шероховатости поверхности детали и величины припуска. Припуск до 2-3 мм срезается за один проход. Если он более 3 мм, то припуск срезается за два прохода: один черновой (предварительный) и второй чистовой (окончательный). Глубина резания при черновом проходе принимается 0,75-0,85 от припуска.
При наружном точении и расточке внутренних отверстий
t= 
где D — диаметр обрабатываемой поверхности, мм;
d — диаметр обработанной поверхности, мм.
При подрезке торца глубину резания принимают от 1 до 2 мм, а при отрезании глубина резания принимается равной длине режущей кромки отрезного резца.
Подача s, мм/об, — величина перемещения режущей кромки резца за один оборот детали. Она зависит от требуемого класса шероховатости, механических свойств обрабатываемой детали и свойств режущего инструмента. Численные величины подач при черновой и чистовой обработках приведены в таблицах справочников и общемашиностроительных нормативов, указанных в рекомендуемой литературе.
Практически подача для обработки стали принимается
— при черновой обработке > 0,3 мм/об;
— при чистовой обработке < 0,3 мм/об.
Для обработки чугунов и других хрупких материалов:
— при черновой обработке > 0,4 мм/об;
— при чистовой обработке < 0,4 мм/об.
Выбранная подача должна быть скорректирована по паспорту металлорежущего станка. Необходимо соблюдать условие, чтобы
Sст < S.
Расчетная скорость резания при точении Vp, м/мин вычисляется по эмпирической формуле:

где Cv — коэффициент, зависящий от качества обрабатываемого материала и материала режущей части инструмента;
Кv — поправочный коэффициент, учитывающий реальные условия резания;
Т — принятый период стойкости инструмента, мин. m, Хv, Yv — показатели степени.
Поправочный коэффициент
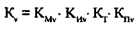
где KMv—поправочный коэффициент, учитывающий влияние обрабатываемого материала;
КИv — поправочный коэффициент, зависящий от материала режущей части инструмента (табл. 2);
Кг — поправочный коэффициент, учитывающий влияние периода стойкости резца (табл. 3);
KПv — поправочный коэффициент, учитывающий сост ояние поверхности заготовки (табл. 4).
Таблица 2
Марка
твердого сплава
|
| Марка
твердого сплава
| KИv
| Т5К10
| 0,65
| ВК8
| 1,00
| ,Т15К6
| 1,00
| ВК6
| 1,20
| Т30К4
| 1.50
|
|
| При точении резцом, оснащенным твердым сплавом, для стали

для чугуна
Значения предела прочности и твердости обрабатываемых материалов находят в справочных данных.
Таблица 3
Стойкость резца Т, мин
| К,.
| Стойкость резца Т, мин
| Кт
|
| 1,15
|
| 0,94
|
| 1,06
|
| 3,92
|
| 1,00
|
| 0,87
|
Таблица 4
Обрабатываемый
материал
| Предел
прочности,
МПа
| Твердость НВ, Мпа
| КПу для заготовки
| с коркой
| без корки
| Углеродистые,
| 400-500
| —
| 1,76
| 2,20
| легированные,
| 500-600
| -
| 1,35
| 1,69
| стальное
| 600-700
| -
| 1,03
| 1,29
| литье
| 700-800
| —
| 0,80
| 1,00
|
| 800-900
| -
| 0,65
| 0,81
| Чугун
|
| 1400-1600
| 1,13
| 1,51
| серый
| -
| 1600-1800
| 0,91
| 1,21
|
| -
| 1800-2000
| 0,75
| 1,00
|
| -
| 2000-2200
| 0,64
| 0,85
|
Определив поправочный коэффициент, находят скорость резания в зависимости от принятых значений стойкости, глубины резания и подачи (по станку). Значения Cv, Xv, Yv, m приведены в табл. 5.
Скорость резания находят для каждого перехода. При точении фаски ее принимают по диаметру, на котором происходит обработка. При обработке конических отверстий скорость резания рассчитывают по наибольшему диаметру конуса.
Таюлица 5
Обрабатываемый материал и его механические свойства
| Подача,
мм/об
| Cv
| xv
| Yv
| m
| Сталь
| S < 0,3
|
| 0,15
| 0,20
| 0,2
|
| S > 0,3
|
| 0,15
| 0,35
| 0,2
| Серый чугун
| S < 0,4
|
| 0,15
| 0,2
| 0,2
|
| S > 0,4
|
| 0,15
| 0,4
| 0,2
|
После определения расчетной скорости резания необходимо проверить возможность осуществления ее на выбранном станке.
Для этого следует найти значение расчетной частоты вращения шпинделя станка пр, об/мин:

где Vp — расчетная скорость резания, м/мин;
D — диаметр обрабатываемой поверхности, мм.
Полученное значение расчетной частоты вращения шпинделя сравнивают с имеющимся на станке и принимают ближайшее минимальное (см. приложение) пст< пр.
Необходимо отметить, что на практике при черновой обработке на любом токарном станке частоту вращения шпинделя не применяют более 500-600, а при чистовой не более 800 об/мин.
По принятому значению частоты вращения шпинделя псг находят фактическую скорость резания Vф,м/мин:
Не нашли, что искали? Воспользуйтесь поиском:
|