Угольным электродом.
Н.Г. Славянов в 1888 г. - метод дуговой сварки плавящимся
металлическим электродом.
Особые заслуги в создании, внедрении, автоматизации современных методов сварки принадлежат ученым НИИ электросварки АН УССР им. академика Е.О. Патона (создание автоматизированных сварочных стендов, конвейеров, промышленных сварочных роботов, сварки в космосе и т.д.).
Сварка - это технологический процесс получения неразъемных соединений металлов и сплавов на основе сил межатомного сцепления свариваемых материалов.
Сварку можно осуществить двумя способами: плавлением и давлением. В первом случае кромки свариваемых деталей расплавляют до получения общей сварочной ванны, которая при охлаждении застывает и превращается в сварной шов. Во-втором случае сварка осуществляется за счет диффузии атомов (взаимопроникновения) двух свариваемых деталей при приложении к ним большого давления, обеспечивающего возможность возникновения между деталями межатомных связей.
В настоящее время используется множество видов сварки, все они классифицированы по различным признакам. Основой классификации (стандартной) является классификация по физическим признакам (рис.16).
В промышленности наиболее широкое применение получили электросварка (электродуговая, плазменная, электрошлаковая) и электромеханическая сварка (контактная, диффузная). Из химических методов наибольшее значение имеет газовая сварка. Из механических способов широко используется ультрозвуковая и трением.
В зависимости от степени автоматизации процесса различают ручную, полуавтоматическую и автоматическую сварку. При сварке автоматизируются обычно процессы подачи присадочного материала и флюса, а также управления источником энергии.
Электродуговая сварка. Для плавления кромок свариваемых деталей при электродуговой сварке используется электрическая дуга, которая может обеспечить высокую температуру (до 6000°С) и большую силу тока в зоне разряда.
Электрическая дуга возникает между двумя электродами, один из которых является свариваемой деталью (1), а второй – специальный стержень (2) рис. 17. Такой способ называют сваркой дугой прямого действия или зависимой дугой. Независимая электрическая дуга горит между двумя стержневыми электродами (рис18).
Для питания дуги может использоваться постоянный или переменный ток. Однако при постоянном токе увеличивается расход электроэнергии, оборудование более громоздко, хотя в этом случае достигается более высокая устойчивость горения дуги.
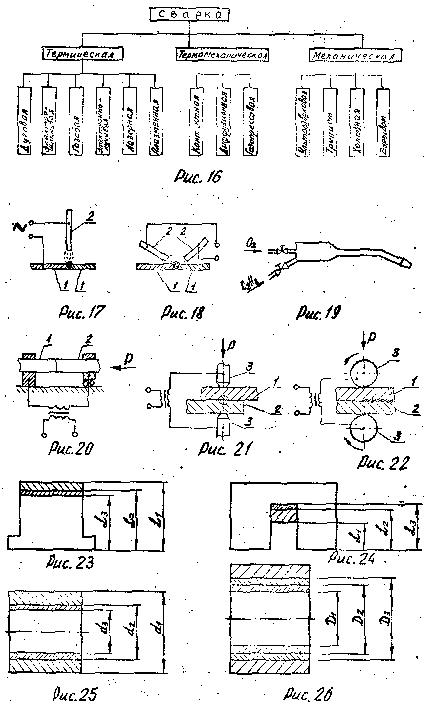
Электрическая дуга на переменном токе менее устойчива из-за непрерывного изменения направления тока, в результате чего дуга может гаснуть. Стабильность дуги повышается при применении переменного тока повышенной частоты (150-450 Гц) или использовании специальных стабилизирующих покрытий, наносимых тонким слоем на электродные стержни. Такие покрытия обеспечивают ионизацию дугового столба и тем самым предотвращают угасание дуги. Электродуговая сварка на переменном токе имеет наибольшее распространение. При этом применяют сварочные трансформаторы, понижающие напряжение до 60-65 В.
Электродуговая сварка выполняется плавящимися металлическими электродами (по способу Славянова) или неплавящимися графитовыми (по способу Бенардоса) или вольфрамовыми электродами. Неплавящиеся электроды служат только для поддержания горения дуги, которая расплавляет кромки свариваемых деталей, образуя сварной шов.
Размеры всех электродов стандартизованы. Плавящиеся электроды для ручной сварки изготовляют из специальной сварочной проволоки, по химическому составу близкой к химическому составу металла свариваемых деталей. Их выпускают с покрытием (обмазкой), которое служит для защиты расплавленного металла от насыщения его кислородом и азотом, создания устойчивости горения дуги, обеспечения легирования металла сварного шва и придания ему свойств, близких к основному металлу.
Электродуговая сварка выполняется открытой или закрытой дугой. Она может быть ручной, полуавтоматической и автоматической. При ручной сварке электрод перемещают вдоль сварного шва по мере его расплавления обеспечивают постоянство длины дуги в процессе сварки. Качество сварного шва зависит от постоянства длины дуги, поэтому при ручной сварке оно неоднородно по длине шва. В этом случае трудно также осуществить защиту дуги, а сварка открытой дугой приводит к образованию оксидов металла на поверхности, газонасыщеенности, рыхлой структуре и снижению механических свойств сварного шва. Повышение качества сварного соединения обеспечивается электродуговой сваркой защищенной дугой, при которой в качестве защитных сред используются флюсы или защитные газы (аргон, углекислый газ и др.)
При сварке таким способом дуга горит под толстым слоем флюса, защищающем расплавленный металл от воздействия окружающей среды и предотвращающем его разбрызгивание, что улучшает условия формирования шва между двумя свариваемыми частями. В состав флюсов входят раскислители и отдельные легирующие элементы, улучшающие структуру, механические свойства сварного шва. Флюс в виде гранул засыпается в зону сварки из бункера. Расплавляясь в процессе сварки, он равномерно покрывает шов, образуя при остывании твердую корку шлака на его поверхности. Впоследствии шлаковая корка легко удаляется.
Основными преимуществами автоматической электродуговой сварки под флюсом являются: повышение качества шва, обеспечение однородности качества шва по его длине, повышение производительности сварки в 10-15 раз по сравнению с ручной, уменьшение расхода электроэнергии и электродной проволоки, улучшение условий труда, уменьшение выделения пыли и газов, отсутствие светового излучения. Но автоматическую сварку нельзя применять для вертикальных, потолочных и фасонных швов.
Газовая сварка. При газовой сварке для расплавления кромок свариваемых заготовок и присадочной проволоки используют теплоту, выделяемую при сгорании газа в кислороде (ацетилена, водорода, пропана, природного газа и др.). Наибольшее применение находит ацетилен, обладающий высокой теплотой сгорания и дающий наибольшую температуру пламени (3150°С).
Для смешивания газов в заданном соотношении и получения устойчивого газового пламени применяют сварочную горелку, в которую газы подаются по шлангам от баллонов (рис.19).
Газовая сварка имеет значительно меньшее распространение, чем электрические методы сварки, т.к. наличие кислорода в пламени ухудшает механические свойства металла и качество сварного шва. Газовая сварка уступает другим методам и по производительности. Этот процесс трудно поддается автоматизации и выполняется в основном вручную.
Газовая резка металлов. Газовую резку обычно используют при раскрое листовой стали, профильного проката и получения фасонных заготовок. Она позволяет разрезать заготовки толщиной до 300 мм.
Газовая резка выполняется специальными режущими горелками-резаками, которые отличаются от сварочных горелок более массивным видом. Резка может быть ручной и машинной. При машинной резке (в серийном и массовом производстве) механизировано перемещение резака, что повышает точность и производительность процесса.
Электрическая контактная сварка. При этом методе свариваемые заготовки предварительно нагреваются электрическим током большой плотности, проходящим черезих поверхности. Сила тока достигает сотен и тысяч ампер, происходит интенсивное выделение теплотыв месте контакта свариваемых поверхностей, металл переходит в пластическое, а иногда расплавленное состояние. После этого ток отключают и осуществляют сжатие свариваемых заготовок, способствующее взаимодействию атомов металлов и образованию сварного соединения. Различают три основных вида электрической контактной сварки: стыковую, точечную и шовную.
Стыковая сварка, при которой свариваемые части (1 и 2) соединяются встык (рис.20). Стыковая сварка разделяется на сварку сопротивлением и сварку оплавлением. При сварке сопротивлением предварительно сжимается заготовки для обеспечения контакта, а затем включается электрический ток, а при сварка оплавлением заготовки сближают при включением электротоке, в результате чего происходит постепенный контакт свариваемых поверхностей. При этом методе меньше расход электроэнергии, а также он дает лучшее качество сварного шва.
Точечную сварку применяют для соединения заготовок внахлестку, свариваемых в отдельных точках. В зависимости от количества пар электродовна сварочной машине можно одновременно получить одну или несколько точек. Свариваемые заготовки (1 и 2) сжимаются между двумя медными стержневыми электродами (рис.21) и включается электрический токна 0,01-1,5 секунд. В месте стыка заготовок, где возникает высокая температура, металл переходит в пластичное или расплавленное состояние. После включения тока сжатие снимается и образуется сварная точка в виде литого ядра.
При шовной сварке свариваемые заготовки (1 и 2) соединяемые внахлестку, зажимают постоянной силой между двумя медными электродами, выполненными в виде вращающихся роликов (3) (рис.22). Роликовая сварка аналогична точечной, но она предназначена для получения непрерывного сварного шва, состоящего из ряда последовательных, перекрываемых сварных точек.
Не нашли, что искали? Воспользуйтесь поиском:
|